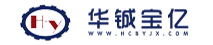
长期以来,各油田普遍采用直接掩埋法处理联合站清罐产生的含油污泥,该方法需占用大量的土地,且掩埋后的污泥中的原油及化学药剂短时间内无法分解,原油在土壤中渗透扩散,会造成更大范围的污染。近年来相继出现的焚烧法、生物法、溶剂萃取法、采用含油污泥制备建筑材料等方法因种种原因均未能大范围推广。
人们目前对含油污泥无害化处理的研究普遍集中在化学法污泥系统脱稳加机械分离这一方法上。结合固液离心分离技术的特点,对含油污泥进行絮凝处理,并采用旋流分离器、螺旋离心机等设备对其进行固液分离,使污泥中的油类物质含量由原来的23%降至0.3~1.5%,污泥再经自然干化后可用于铺垫道路和井场。其中,采用螺旋离心机处理后的污泥中油类物质的含量为0.3%,可作为农用污泥直接排放。旋流分离器的平均分离效率为91.6%,螺旋离心机的平均分离效率为98.38%。
1 含油污泥处理流程
本文设计了含油污泥无害化处理的中试流程,其中的机械分离装置采用旋流分离器,后根据中试取得的数据设计了螺旋离心机,并模拟现场使用条件进行了性能对比试验。
根据含油污泥的特点,吸泥机入口设置了机械旋转格栅,栅格间距5mm,通过格栅的翻转可将混入污泥中的大颗粒物体、飘落至污泥池中的条形杂物带出。
吸泥机提取的污泥通过热交换器进行加热,使之达到50℃左右。加热后的含油污泥进入搅拌罐,添加3.5~4倍的油田热污水,污水温度在50℃左右,在其中加入0.1%左右的自制化学药剂,该化学药剂以平均分子量为400~1000万的阳离子型聚丙烯酰胺为主,由于残留在污泥中的化学药剂数量较少,避免了二次污染的发生。通过搅拌使污泥系统脱稳,实现油、水、渣三相的基本分离,油、水混合物进入沉降罐进一步分离。沉渣通过旋流分离器进一步除去固相中的液相,实现固液分离。
经过处理后的污泥自然干化排放。污泥清洗、固液分离后的液体进一步沉降分离,残余污水可循环使用。
2 分离效率测试
2.1 旋流分离器
旋流分离器主要由蜗体、尾锥两部分组成,蜗体直径为136mm,尾锥锥角为13°。
取旋流分离器入口处及溢流口处悬浮液各100mL,过滤并干燥,得固体物质分别为20.95g、1.76g,采用XSB-88型顶击式震筛机振动20min后得到的粒度检测结果见下表:
样品目数(粒径/mm) | 入口样品质量(g) | 溢流口样品质量(g) | 旋流器分离效率(%) |
40(0.45) | 4.28 | 0.07 | 98.36 |
100(0.154) | 1.72 | 0.12 | 93.02 |
140(0.105) | 2.55 | 0.21 | 91.76 |
200(0.074) | 8.96 | 0.82 | 90.85 |
300(0.050) | 2.09 | 0.31 | 85.17 |
400(0.0385) | 1.35 | 0.23 | 82.96 |
合计 | 20.95 | 1.76 | 平均91.6 |
注:旋流器分离效率=[(入口处质量-溢流口处质量)×100/入口处质量]%
2.2 螺旋离心机
螺旋离心机主要由转鼓、螺旋输送器、溢流堰、驱动系统、进出料系统和密封润滑系统等几部分组成。转鼓直径为300mm,长径比为4.0,转速为2500r/min。
取现场待处理含油污泥样品30kg,于实验室内模拟现场流程进行试验。加热含油污泥,添加化学药剂,撇去浮油后搅拌使其成为悬浮液,通过螺旋离心机进行固液分离。
取螺旋离心机入口处及溢流堰处悬浮液各100mL,过滤并干燥,得固体物质分别为26.62g、0.43g,得到的粒度检测结果见下表:
样品目数(粒径/mm) | 入口样品质量(g) | 溢流口样品质量(g) | 旋流器分离效率(%) |
40(0.45) | 4.94 | 0 | 100 |
100(0.154) | 2.65 | 0.02 | 99.25 |
140(0.105) | 4.02 | 0.04 | 99 |
200(0.074) | 10.33 | 0.12 | 98.84 |
300(0.050) | 3.12 | 0.16 | 94.87 |
400(0.0385) | 1.56 | 0.09 | 94.23 |
合计 | 26.62 | 0.43 | 平均98.38 |
注:离心机分离效率=[(入口处质量-溢流堰处质量)×100/入口处质量]%
3 结果与讨论
旋流分离器依靠悬浮液本身所有的机械能实现固液分离,而螺旋离心机则依靠外加动力实现固液分离,二者所产生的离心力差异较大,因而分离效率存在差距。对于经旋流分离器与螺旋离心机分离所得到的污泥样品及原始样品采用石油醚溶解法分别测定其中油类物质的含量。结果采用旋流分离器处理后的污泥中油类物质的含量为1.5%(质量百分比),采用螺旋离心机处理后的污泥中油类物质的含量为0.3%。
含油污泥经化学法实现系统脱稳后,仍有少量原油微滴吸附于固体颗粒表面的微孔之中,或局部(全部)润湿铺展于固体颗粒表面,这是由于原油颗粒与固体颗粒间的粘附功大于原油颗粒间的凝聚功所造成的。在随后进行固液离心分离时,固体颗粒发生剧烈碰撞、剪切,当外部机械能大于原油颗粒与固体颗粒间的粘附功时,原油颗粒与固体颗粒脱离,并相互聚集成为较大颗粒的油滴排出。外部机械能越大,固体颗粒间的碰撞就越激烈,因而吸附于固体颗粒表面的原油颗粒就越少。由此可以解释相同条件下经螺旋离心机处理后的污泥中油类物质的含量低于旋流分离器处理后的污泥。
对处理后的污泥进行含油量检测,表明其中仍含有油类物质,这可能是由于残余的吸附于固体颗粒表面微孔中的原油微滴所致,这些原油微滴中的挥发性物质随污泥的干化而挥发,残余的沥青质以更加紧密的方式与泥砂颗粒相结合且难溶于水。如用此污泥铺垫道路或井场,不会在雨季时造成污染。
采用旋流分离器作为分离设备具有设备免维护,无需外加动力,操作简便等特点,设备的本身造价及运行成本都较低,可应用于污泥颗粒较大,对处理后残余污泥的排放要求不高的场合;采用螺旋离心机作为分离设备具有分离效率高,分离粒度小,处理后的污泥含油量低的特点,但设备的本身造价及运行成本都高于旋流分离器。
曾对未处理的含油污泥采用板框式压滤机进行处理,因原油粘度较大造成压滤机滤布孔隙堵塞,无法进行下步工序。考虑到压滤机的设备造价、日常维护成本等问题,在机械分离过程中未采用其替代旋流分离器与螺旋离心机。
4 结论
(1)采用旋流分离器处理后的污泥中油类物质的含量为1.5%,污泥经过自然干化后可以用于铺垫道路和井场。旋流分离器的平均分离效率为91.6%。
(2)采用螺旋离心机处理后的污泥中油类物质的含量为0.3%,污泥可作为农用污泥直接排放。螺旋离心机的平均分离效率为98.38%。
(3)对于污泥颗粒较大,对处理后残余污泥的堆放等要求不高的场合推荐使用旋流分离器。而对于污泥颗粒较小,且对残余污泥的处理要求严格的场合则推荐使用螺旋离心机。