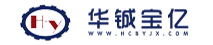
炼油厂污水处理场的“三泥”,是指含油污水均质池的油泥、浮选池的浮渣和生化曝气池的剩余活性污泥。“三泥”中有机污染物成分复杂,恶臭严重,含水率很高,稳定性好,脱水难度大,处理难度大。过去的“三泥”,主要成分是剩余活性污泥,随着废水处理技术的不断发展,剩余活性污泥的产生量越来越少。均质池的油泥产生量一直都很少,这样,浮选池的浮渣成了“三泥”的主要成分,从某种程度上讲,“三泥”即为含有少量油泥的浮渣。
对于总量大、含水率很高的浮渣型“三泥”,脱水是处理的必须环节,尤其是建有焦化装置的炼油厂,脱水是“三泥”处理的关键手段。“三泥”脱水后送焦化装置处理,出水的COD小于或等于2500mg/L(通常讲的“水清”)情况下送污水处理厂。
由于原油品质的变化和废水处理工艺的改进,导致了“三泥”构成与性状的变化,使得一些炼油厂的“三泥”离心处理效果日益恶化,为此有必要对新形势下的“三泥”性状与离心处理工艺作一个系统调查与优化。
1 “三泥”性状
根据统计结果,一个加工原油1×107t/a的炼油厂,以浮渣为主的“三泥”产生量为30~60t/d,原始浮渣(主要是指从浮选池刮下自流到集泥池后每天泵入“三泥”储罐过程中在进入储罐前的管道上采集的浮渣)的性状在一定时间内相对稳定,而待处理浮渣(是指经过“三泥”储罐收集汇总后自流至三相离心设备的混合浮渣)由于经过“三泥”储罐混合、自然沉降分层、冲混等一系列复杂过程,其性状波动较大,主要表现在因罐内分层导致处理物料随出料液位的变动而变化,另一方面,浮渣性状也会随被处理废水的水质变化而产生阶段性波动。
与此同时,对当时的新鲜浮渣的沉降性能进行了测试。将新采集的500mL浮渣样品倒入500mL的具塞量筒中,使其自然静止沉降分层。
浮渣在8h之内基本无分层或分层较少,而且分层呈现无序性,有时渣在下层,有时渣在上层;当渣在下层时,水层表面有一薄油层。
由此可见,新鲜浮渣的表观较厚,含水率平均为91.2%,含油率平均为4.36%,自然沉降较为困难,8h时很少分层,24h时分出的水层体积平均为11%,而且水、渣层分布呈无序状。
2 优化试验结果
污水处理场“三泥”处理工段现场的工况:均质池油泥阶段性产生,直接进入干泥池;剩余活性污泥基本不产生;浮渣通过刮渣后排入浮渣井,用离心泵将其打入容积为500m³的浮渣罐中,在罐出口(离罐底1.5m)用螺杆泵将其送至三相离心机进行离心处理,出水返回污水处理场,脱水后的污泥与均质池油泥一起送焦化装置处理。
针对“三泥”性状,以离心机转速和差转速、絮凝剂投加量、“三泥”中灰分含量、絮凝剂牌号等作为试验考察参数,按照现有工况和处理设施进行现场考察试验。
2.1 离心机转速对“三泥”处理效果的影响
由于当时尚未知道絮凝剂的较佳投加量,在以为其投加量肯定不足的思维下选定的工况:“三泥”处理量4.0t/h,差转速10r/min,投加质量分数为0.15%的Z7650絮凝剂(进口药剂)400L/h。在确保“三泥”组成相对稳定“含水率97%,灰分0.31%左右,下同)的前提下,只调节离心机转速,考察其对“三泥”处理效果的影响。
在其他条件一定时,在本试验选用的离心机转速范围内,离心机转速在1500~3000r/min时与“三泥”处理效果存在着明显的负相关性,离心机转速越小处理效果反而越好;当离心机转速达到1500r/min时,对“三泥”处理效果的改进作用趋于平稳。再进一步考察后发现,离心机较佳转速为1300r/min。
2.2 絮凝剂投加量对“三泥”处理效果的影响
本试验的固定工况:“三泥”处理量4.0t/h,离心机转速2000r/min,差转速10r/min,絮凝剂为质量分数0.2%的Z7650。试验中只调节絮凝剂投加量,考察其对“三泥”处理效果的影响。
絮凝剂投加量对“三泥”处理效果的影响较大,在上述工况下处理灰分为0.3%左右的“三泥”时,质量分数0.2%的Z7650絮凝剂投加量为50~100L/h时“三泥”的处理效果较好,其投加量超过100L/h时“三泥”的处理效果反而下降。
2.3 “三泥”中灰分与絮凝剂投加量的配比对“三泥”处理效果的影响
本试验的固定工况:“三泥”处理量4.0t/h,离心机转速2000r/min,差转速10r/min,絮凝剂为质量分数0.2%的Z7650。进行“三泥”中灰分与絮凝剂投加量的配比试验,考察其对“三泥”处理效果的影响。
当“三泥”中的灰分达到0.4%以上时,质量分数为0.2%的Z7650絮凝剂50L/h的投加量就不够了。灰分越高,要达到较好的处理效果所需投加的絮凝剂量也相应增加。
2.4 国产絮凝剂对“三泥”处理效果的试验
选用了一种国产的双组分絮凝剂(A+B)作了相同的参数优化试验。用与上述试验同样的“三泥”,在适合该絮凝剂的较优工况(“三泥”处理量4.0t/h,离心机转速2000r/min,差转速10r/min,絮凝剂投加量:质量分数2%的组分A为130L/h+质量分数2%的组分B为130L/h)的条件下进行“三泥”处理试验。
在稳定的工况条件下(“三泥”中灰分为0.30%~0.36%),国产双组分絮凝剂在适合其较优工况时,对“三泥”的处理效果与现用的进口絮凝剂相仿,但成本更高。
3 讨论
3.1 处理效果与稳定性
现场试验结果表明,目前情况下“三泥”离心处理的理想条件是:“三泥”处理量4.0t/h,絮凝剂Z7650的投加量按0.2%(质量分数)计为50L/h,离心机转速1300r/min,差转速10r/min。为了考察“三泥”处理效果的稳定性,进行了为期2d的连续采样分析。
在上述条件下处理灰分为0.25%~0.30%的“三泥”时,出水的COD可以保持在1000mg/L以下,达到预定的COD小于2500mg/L的处理要求。而相同絮凝剂Z7650的投加量可从原来的0.15%(质量分数)计200L/h减少到现在的0.2%(质量分数)计50L/h,絮凝剂用量降幅超过50%。由此可见,优化操作的效果是明显的。
3.2 离心机转速过大对“三泥”处理效果的影响
污泥悬浮物通过絮凝剂作用而凝结的胶合物,本身不很稳定,在一定的外力作用下又会分开。此胶合物作为整体,它与水体介质存在一定的密度差,在离心力的作用下原来较小的密度差会得到放大,从而达到快速分离。而其内部实际上包含由架桥作用和范德华力等牵引而成的2部分——高分子絮凝剂和含油较高的胶粒,虽然作为整体后其综合密度略大于水,而作为内部个体,含油较高的胶粒的密度比水小,而高分子絮凝剂的密度比水大。因此,随着离心机转速的增大,含油较高的胶粒与高分子絮凝剂的密度差引起的离心力差也随之增大,当该差值大于相对稳定的胶合物内部两组成之间的架桥作用和范德华合力时,絮凝作用失效,胶合物稳定系统被破坏。因此,对于由絮凝作用而凝结的炼油厂“三泥”的离心分离来说,离心机转速过大反而会影响“三泥”的处理效果。
3.3 絮凝剂用量过大对“三泥”处理效果的影响
本试验所采用的絮凝剂是以聚丙烯酰胺为基质的阳离子型有机高分子聚合物,它对于炼油厂“三泥”中胶体粒子的作用主要是通过架桥和电中和产生。当絮凝剂用量过大时,一方面会使胶粒表面的电荷因中和过量而逆转,造成已絮凝的胶体的重新悬浮;另一方面,会对胶粒表面产生保护作用,也会使已解稳的胶体转向再悬浮。因此,絮凝剂投加量过大反而会使已解稳的“三泥”胶体再悬浮,从而影响其处理效果。
4 结论
在目前炼油厂“三泥”主要以浮渣为主且总量相对较小的情况下,考虑到许多炼油厂早已配备有“三泥”离心处理设施,提出处理系统的优化方案为:以原始产生的浮渣为处理对象,利用旧罐或新建一个容积为100m³的污泥贮存均质罐,内部底位安装慢速搅拌机,加药系统保持不变,离心设施不变。运行时,污泥自集泥井来,从罐底泵入污泥贮存均质罐,经过罐中搅拌机的搅拌,达到均质,然后从罐底部自流至离心机进行离心处理;“三泥”处理量为3.5~4.0t/h,以Z7650药剂作为絮凝剂,其用量控制在0.2%(质量分数)计50~100L/h,离心机转速为1300~1500r/min,差转速为10r/min。“三泥”离心处理后,水相返回污水处理场,渣相按照目前处理流程送焦化装置处理,产生的少量污油被回收。