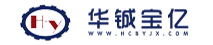
兰州石化公司(以下简称兰州石化)高密度聚乙烯装置采用三井油化淤浆法工艺,装置设计能力未7万t/a。螺旋沉降离心机是该工艺流程中用于分离己烷溶剂和聚乙烯粉料的关键设备。装置投产初期,因转鼓转速过高引起扭矩过高,致使离心机频繁停车,无法正常运转,生产不能连续稳定地进行。
1 离心机概况
装置使用的是吉林化学工业公司(以下简称吉化)机械厂制造的LWF1050-N型螺旋沉降离心机。
主要技术参数(设计值)如下:转鼓转速n=1580r/min;转鼓锥角2α=20°;螺旋升角β=8.2°;排渣能力Q=13t/h;分离因数Z=1465;电机功率N=185kW;电机转速N1=988r/min;差速器比i=80/81;差动转速△n=19r/min;转鼓长高L=1500mm;溢流孔直径h=110mm;转鼓大端直径r1=1040mm;转鼓小端直径r2=820mm;皮带轮直径d=590mm。
装置投产初期,离心机运行不正常,在不到半年的时间里,因各种原因停车多达70余次,其中突出的原因是扭矩过高联锁停车,或因剪切销剪断而跳车。
2 离心机扭矩偏高的原因分析
2.1 理论分析
根据力矩平衡原理,设定逆时针方向为正向,分别对离心机3个传动部件差速器、外转鼓、内转鼓做力矩分析。
在差速器平稳运行时,如果不考虑摩擦损失,整个行星齿轮传动系上力矩代数和应为零,输入和输出功率的代数和也为零。
推料阻力施加给内转鼓的力矩是由聚乙烯粉料沉渣在转鼓锥筒部的离心力与转鼓壁的摩擦力及其与螺旋页面的摩擦力所产生的,由于沉渣在从脱水区大端向小端出渣口运动的过程中,回转半径是逐渐减小的,离心力、螺旋升角和沉渣运动的方向角也随之改变。
离心机的扭矩与分离因数成正比,与负荷成正比。因为分离因数与转鼓转速的平方成正比,与转鼓半径成正比,所以,离心机的扭矩与转鼓转速的平方成正比。
通过以上分析,得出下面结论:在转鼓尺寸一定的条件下,离心机的扭矩受转鼓转速及负荷的影响。在负荷一定的条件下,离心机的扭矩只受转速的影响。
2.2 同类装置离心机参数的比较
兰州石化7万t/a HDPE装置的设计是采用扬子石化公司(以下简称扬子)同类生产线工艺,由于考虑到以后的扩容问题,兰化离心机在设计时生产能力由7万t/a改扩到了10万t/a,处理量由9t/h增加到13t/h。技术参数也做了相应的调整。2套装置离心机的参数大端直径D、转速n、分离因数Z(n²·D/2g)如下表所示:
名称 | D/mm | n/(r/min) | Z | M/kg·m |
扬子离心机 | 1010 | 1450 | 1194 | 8.4 |
兰州石化离心机 | 1050 | 1580 | 1465 | 13.8 |
从2套装置离心机的参数可以看出,兰州石化离心机生产能力的提高在设计上是通过增大转鼓直径及提高转鼓转速来实现的。
离心机转鼓按照 标准,离心机转鼓的基本参数符合下表的规定:
基本型号 | D/mm | n/(r/min) | Z |
LW800 | 800 | 1250~2000 | 700~1790 |
LW900 | 900 | 1000~1600 | 500~1290 |
LW1000 | 1000 | 900~1400 | 450~1100 |
LW1120 | 1120 | 800~1250 | 400~980 |
从上表的参数可以看出,按照卧式螺旋卸料沉降离心机制造的 标准,随着离心机转鼓直径的增大,转鼓转速和分离因数相应地在减小。扬子离心机的基本参数与 标准规定的技术参数基本吻合,而兰州石化离心机的基本参数与国标规定的技术参数相差甚远,转速和分离因数明显偏大,违背了离心机直径越大,转速和分离因数应相应减小的规律。
因此,可以断定离心机故障是转鼓转速过高造成的。
3 改造效果
3.1 改造方案
因为离心机扭矩与分离因数成正比,分离因数与转鼓转速的平方成正比,所以,降低离心机扭矩较便捷的方法是降低转鼓的转速,在电机一定即输入转速不变的前提下,减小电机皮带轮或增大转鼓皮带轮均可降低转鼓转速,但比较而言,减小电机皮带轮的方法更为简单可行。因此,参照其他装置的技术参数,将电机皮带轮直径由原来的590mm降低到530mm。
3.2 改造后扭矩降低情况的理论推算
电机皮带轮减小后,离心机扭矩应有较大降低。以离心机负荷为13t/h(聚合投料量9t/h)为例进行计算,得到2种皮带轮分别对应的转鼓所受总扭矩值及差速器一级太阳轮所受扭矩值如下表所示:
皮带轮直径/mm | 转鼓转速n/(r/min) | 分离因数Z | 扭矩M/kg·m | 扭矩M1/kg·m |
590 | 1580 | 1162 | 1057.6 | 13.1 |
530 | 1434 | 955 | 869.2 | 10.7 |
上表所列数据是忽略了液相己烷对转鼓产生的扭矩,且将渣料湿含量看作均衡的30%计算得出的。由于液相己烷也会对转鼓产生微小的扭矩,渣料湿含量在整个出料段是逐渐降低的,在出料段起始部分其湿含量要远远高于30%,所以,上表所列扭矩值比实际扭矩值要稍偏低。
由上表可见,皮带轮直径改小后,分离因数降低近20%,离心机扭矩M1降低了约19%。
3.3 改造后实测扭矩
电机皮带轮减小后,在负荷为13t/h时,实际测得离心机扭矩M1保持在9.5~10.8之间,与上表计算值基本吻合。
4 结论
(1)兰州石化7万t/a HDPE装置离心机的扩容设计选用转速偏高,超出了离心机转速规定指标,由此引起了设备在投运后的一段时间内无法正常平稳运行。
(2)在保证目前生产负荷13t/h的前提下,设备转速由1580r/min降低为1434r/min,从根本上改善了离心机的运行状况,运行周期长达半年以上。由此可见,对离心机故障的原因分析是准确的,改造的费用不高,措施简单,实用有效,达到了预期的目的。
(3)改造后渣料湿含量无明显增大,也能满足7万t/a的生产能力。但改造后机组实际上负荷能达到多少,改造后是否会带来其他问题,还有待于进一步考核。