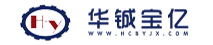
含油污泥是石油勘探、开采、炼制、加工、储存、运输等过程中产生的主要固体废弃物之一。含油污泥中不仅含有大量原油、蜡质、沥青质、胶质等,还含有苯系物、酚类、蒽、芘等有毒有害物质,若处理不当,会产生严重的环境污染,是影响油田及周边生态环境、威胁人类健康的重要污染物之一,已被许多 列为危险废弃物。随着自然资源的逐渐减少和全球固体废弃物排放量的进一步增加,许多 都加大了对固体废弃物的资源化再利用。由于含油污泥中含有丰富的碳氢化合物,使油泥资源化利用成为可能。但油泥中大量重质油与泥沙及水形成稳定的悬浮乳状液体系,黏度大、乳化程度高,处理难度大。因此,含油污泥的资源化处置一直是困扰石化行业的重大技术难题。
目前,含油污泥的处理方式主要有溶剂萃取、堆肥、生物降解、热解、焚烧等,但现有处理技术存在处理效果不理想,处理费用高,产生二次污染,不适于规模化工业应用等缺点。油泥调质-机械分离处理技术是通过添加有机溶剂、破乳剂、表面活性剂降低油/水界面膜强度,再利用离心设备产生强大的离心力促使不同密度的组分(例如水、油、固体渣)在短时间内分离,具有能耗低,污染小,操作简单等优点,适合油泥资源化处理工业化应用。在阎松等的研究中,就利用加热预处理降低油泥黏度,并向油泥中添加了十二烷基苯磺酸钠、碳酸钠、聚丙烯酰胺复配药剂,在3000r/min转速下离心20min,油泥脱水率可达92.17%。而CAMBIELLA等的研究则发现小剂量添加促凝剂CaCl2可以提高油泥离心油水分离效果,油分离效率可达92%~95%。然而,国内外对调质-机械分离技术的研究仅局限于单一或少数油泥样品,通用性差,难于工业化应用。因此,研究并开发一套适用性强、效率高、可工业应用的油泥资源化处理集成技术势在必行。
为实现高效率、低成本、大规模处理油泥,从2012年开始,浙江大学联合舟山纳海固体废物处置有限公司开展了共同研究,设计出含油污泥2级分离处理系统。经过先导实验、中试实验、规模化测试及工艺优化实验,完成了含油污泥资源化处置方案制定和流程设计。目前,已建成日处理100t/d的油泥资源化集成技术示范工程。本文基于实验室研究,着重讨论了2级分离系统各阶段的分离效率及工艺优化,对油泥调质药剂选择、掺混溶剂优化等进行了详细探讨,可为今后含油污泥资源化利用提供有力的技术支持。
1 材料和方法
1.1 含油污泥分选与处理工艺说明
1.1.1 油泥样品成分分析及处理工艺设计
含油污泥水、油、渣3组分含量确定了油泥资源化利用价值和处理方案选择。为了建立适用性广、分离效率高的油泥资源化处理工艺,选取了来自 各地的10种油泥样品进行了3组分成分测定和先导分离实验,并对不同成分的油泥进行了处理工艺分类。10种油泥的3组分含量见表1。
表1:含油污泥水、油、渣3组分含量
序号 | 来源 | 水/% | 油/% | 渣/% | 类型 |
1 | 中化兴中石油转运有限公司清罐油泥 | 32.2 | 66.2 | 1.6 | Ⅰ |
2 | 非洲乍得含油污泥 | 13.8 | 30.5 | 55.7 | Ⅱ |
3 | 纳海固体废弃物处置有限公司回收油泥 | 17.3 | 80.3 | 2.4 | Ⅰ |
4 | 中国石化集团杭州炼油厂 | 45.1 | 52.8 | 2.1 | Ⅱ |
5 | 纳海固体废弃物处置有限公司油污水底泥 | 22.8 | 52.1 | 25.1 | Ⅱ |
6 | 百达石油有限公司含油污泥 | 24.2 | 45.2 | 30.6 | Ⅱ |
7 | 日本船舶清舱油泥 | 12.9 | 38.0 | 49.1 | Ⅱ |
8 | 舟山益民废物利用厂回收油泥 | 18.9 | 35.9 | 45.2 | Ⅱ |
9 | 中海石油舟山石化有限公司油泥 | 24.9 | 30.1 | 45.0 | Ⅱ |
10 | 海通船舶清舱油泥 | 22.3 | 38.7 | 39.0 | Ⅱ |
含水量约为13%~45%、含油量约为30%~80%、含渣量约为2%~55%。依据先导分离实验效果,按照油泥3组分构成,将油泥处置工艺方案分为Ⅰ型、Ⅱ型、Ⅲ型、Ⅳ型4种,见表2。
表2:含油污泥处理方案分类
类型 | 处理工艺方案 |
Ⅰ型 | 加热降黏脱渣后,进行化学调质破乳,再经离心机进行三相分离。适用于含油率高,含渣量少油泥。 |
Ⅱ型 | 需加入轻质油加热降粘进行大颗粒脱除,再进行化学破乳及离心回收油,适用于水油渣三组分含量适中油泥。 |
Ⅲ型 | 适用于含水量较高油泥,需静置待自由水分离后,再按Ⅰ型或Ⅱ型油泥进行处置。 |
Ⅳ型 | 含油量较小油泥资源化利用回收价值低,直接无害化焚烧处理。 |
Ⅰ型适用于含油量高、含渣少、黏度低、高回收价值油泥,加热至一定温度即可使油泥中的固体渣自然沉降,脱除固体渣后,仍需加入破乳剂破乳以实现三相的完全分离。油泥含油量大于60%且含渣量小于15%适合Ⅰ型方案。Ⅱ型适用于常见油泥类型,3组分需在油泥中添加轻质油、加热降黏进行大颗粒脱除预处理,再进行化学调质实现三相分离。含油污泥中水、油以稳定的油包水形式存在,通常乳化水含量在60%以下,含量高于60%的油泥可能存在一定比例的游离水。Ⅲ型适用于此类高含水油泥,需将油泥样品静置待游离水分离后,再依照Ⅰ型或Ⅱ型进行处置。对于含油量小于20%的油泥,资源化利用价值低,不适应用三相分离方式处理油泥。Ⅳ型建议采用焚烧等其他无害化处理方式处理含油量低的油泥。
根据不同油泥处理方案需求,设计了含油污泥2级分离处理系统,主要包括高含固预处理(HSPU)一级分离系统和化学调质(CCSU)二级分离系统。Ⅰ型、Ⅱ型、Ⅲ型处理方案都可以在2级分离系统中实施。
1.1.2 高含固预处理一级分离系统
针对油泥样品含固率高及黏度大的特点,处理系统中设计了高含固预处理单元实施油泥一级分离。在HSPU中,蒸汽锅炉产生的蒸汽作为油泥加热源,通过蒸汽加热、搅拌可降低油泥的粘度,使粗颗粒与油水混合液有效分离。油泥中的石蜡组分在70℃以上可以完全熔化,所以工艺设计蒸汽加热温度至75℃左右,以保证油泥在处理输送过程中有很好的流动性。为了保证生产安全和能源高效利用,蒸汽加热后油泥温度不应超过80℃。为确保油泥由室温升至75℃并保持内部温度分布均匀,加热搅拌时间设置为1~2h。为了使HSPU能有效地分离粗颗粒,加热后油泥的粘度应降至1.0Pa·s以下。如果油泥黏度达不到要求,则将含油污泥与轻质油按一定比例掺拌混合降低黏度,改善油泥的分离特性。油泥与热蒸汽、轻质油混合搅拌的过程中,悬浮大颗粒由于密度差自然沉降于底部,在HSPU处理池中,设计有刮板输送机对大颗粒固体渣进行一级分离。HSPU对固体渣的脱除率大于85%。一级分离后,具有较好流动性的油水混合物将输送至二级分离系统进行进一步分离。
1.1.3 化学调质二级分离系统
二级分离系统主要包括化学破乳调质池、三相分离离心机。依据油泥中水油乳化特性,选择微乳液作为破乳剂,按一定比例加入调质池混合。调质后油水混合物进入三相卧螺离心机进行脱水、脱渣处理。三相离心机分离后,油泥中残留的小颗粒渣相与油相完全分离并从离心机排渣口连续排出。油泥中的乳化水滴在离心机中聚并形成自由水从排水口排出。离心机出料口流出的是较为纯净的回收油,含水、固体颗粒重量比小于3%。分离得到的水相进入隔油池去除浮油,再经膜处理净化后可进入蒸汽锅炉回用,固体渣将进行焚烧无害化处理。
1.2 含油污泥样品
选择适用Ⅱ型处理的典型油泥,5号纳海固体废弃物处置有限公司油污水底泥作为实验样品,3组分含量见表1,模拟含油污泥2级分离系统工艺流程,在实验室进行含油污泥2级分离系统工艺优化研究。
1.3 实验方法
为掌握不同轻质油掺混比例、微乳液添加比例等工艺参数组合情况下,含油污泥2级处理系统脱水、除渣效率,编制了实验室工艺优化测试方案。
1.3.1 掺混轻质油实验
将300g油泥置于500mL烧杯中进行75℃水浴加热,模拟一级分离系统中HSPU反应池。实验选用煤油、甲苯、柴油为掺混油,在油泥中分别添加5%、10%、20%轻质油,由电动搅拌器搅拌1h,使得油泥与轻质油充分混合,促进固体颗粒沉降。
1.3.2 微乳液配制及添加实验
微乳液是由油、水、表面活性剂及助表面活性剂在一定条件下自发形成的热力学稳定体系。实验中所用微乳液均按照SCHULMAN法来配制,即将一定比例的油相、水及表面活性剂混合均匀,然后向体系中加入助表活面活性剂,直至体系澄清透明,即形成微乳液。采用壬基酚聚氧乙烯醚(NP-10)为表面活性剂,乙醇、异丙醇、正丁醇为助表面活性剂,甲苯、煤油为油相,去离子水为水相配制微乳液。实验所用试剂均为分析级。
一级分离后,取上层油水混合物于烧杯并加入5%质量比的微乳液,搅拌15min后,进行离心分离。二级离心分离在实验室离心机Thermo Scientific ST40上进行,在3040g(g为重力加速度)分离因数下,离心分离20min。离心分离因数及停留时间设置都与规模化离心机可达到的离心参数设置一致,每组实验重复进行2次,以确保工艺优化实验数据具有可比性、可靠性。
1.4 测量指标及方法
油泥含水量依据ASTM-D95-05标准方法测定;含油量依据索氏提取法测定,溶剂选用甲苯;含渣量通过差减法计算得到。表观黏度采用数字式旋转黏度计,型号为Brokkfield,Model RVDV-Ⅱ+P,测量中选用RV-5号转子,并在10r/min转速下测定。Olympus BX53光学显微镜用于观察W/O型石油乳化液的微观结构。固体渣粒径分布由Mastersizer 2000激光粒度仪测定。
传统的光学粒径测量技术不能分辨出油泥中的乳化水,因为油泥颜色黑且不透光。在实验中,采用基于差示扫描量热法(DSC)测量石油乳化液水滴粒径分布的技术。DSC测试在梅特勒托利多型号为DSC1的差热扫描量热仪上进行,氮气作为吹扫气流量设定为60mL/min,样品的降温速率为5℃/min,直至样品中所有的乳化水冻结。
2 结果与讨论
2.1 一级分离系统工艺优化
Ⅰ型油泥含油率高,含固率低,油泥黏度低,可经一级分离系统加热后直接进入二级分离单元,而Ⅱ型油泥黏度高、含渣率大,为保证二级离心分离效果及离心机运行稳定,需对入口油泥进行掺混轻质油加热预处理,降低油泥的黏度及含固率。
2.1.1 掺混轻质对含油污泥降粘效果影响
轻质油与油泥充分混合互溶后,可有效降低油泥粘度及流动阻力。油泥掺混轻质油后测定其粘度,结果见表3。
表3:不同添加量下轻质油的降黏效果
轻质油 | 添加质量比/% | 黏度ηc/(Pa·s) | V/% |
煤油 | 5 | 4.27 | 69.1 |
煤油 | 10 | 1.98 | 85.6 |
煤油 | 20 | 0.63 | 95.4 |
甲苯 | 5 | 4.72 | 65.8 |
甲苯 | 10 | 2.30 | 83.4 |
甲苯 | 20 | 0.81 | 94.1 |
柴油 | 5 | 6.66 | 51.8 |
柴油 | 10 | 3.50 | 74.6 |
柴油 | 20 | 1.59 | 88.5 |
为了评价不同轻质油及不同添加量的降粘效果,引入降黏系数V,其定义式为:
V=(ηr-ηc)/ηr×100%
式中:ηr为原始油泥的黏度,ηc为添加轻质油后油泥的黏度。油泥原样在测试温度下,黏度为13.80Pa·s,添加5%煤油后,黏度下降明显,降黏系数V可达69.1%。当煤油添加量为10%时,黏度进一步降低至2Pa·s以下。当添加量提高到20%时,在75℃的环境下,黏度较原样可下降95%以上,并具有很好的流动性。当油泥与甲苯掺混时,其黏度变化趋势与添加等量煤油时相似。由此可见,煤油和甲苯对油泥中的油相组分均有较强的溶解能力。溶剂对油泥的溶解能力遵循与溶剂的溶解度参数δ越接近,溶解性越高的“相似相溶”规律。
甲苯可以与油相有机组分相溶,特别是与重质沥青质可以互溶,而煤油含有20%~50%的芳香族化合物,对油泥中重组分胶质、沥青的互溶能力较强,所以降黏效果明显。柴油是碳原子数约为10~22的烃类混合物,对油泥中重质组分溶解能力较弱,其降黏效果略逊于煤油和甲苯,当添加20%柴油时,V值为88.5%,仅略大于煤油添加10%时的降黏系数。综上所述,甲苯与煤油的降黏效果好于柴油,但甲苯毒性大,考虑到大规模应用的成本及安全性,从添加轻质油降黏角度考虑,选择煤油作为较佳轻质油。同时,对于其他适合Ⅱ型处理的油泥样品,可根据样品黏度、二级离心机对入口油泥黏度要求、轻质油降黏系数V来确定较佳添加量。
2.1.2 掺混轻质油对油泥一级脱渣效率影响
油泥中悬浮的固体颗粒主要是石英、金属氧化物、碳酸盐及其他矿物。油泥样品中固体颗粒的粒径范围在2~831μm之间。由斯托克斯定律可知,固体颗粒在连续相中沉降速度主要制约于连续相的黏度,掺混轻质油并加热有效降低了油泥的黏度,因此可大幅度提高固体颗粒一级分离效果。
不同比例掺混轻质油,油泥脱除固体渣的分离效率结果表明,当油泥掺混5%煤油时,可实现31.7%的脱渣率。添加10%煤油时,一半以上的固体颗粒可通过密度差自然沉降于底部。煤油掺混比例至20%时,沉降后固体颗粒可脱除91.2%。油泥与5%、10%、20%甲苯的掺混物加热沉降后,固体颗粒分离效率可分别达到28.3%、58.6%和88.5%。柴油的降粘效果不及煤油、甲苯,所以其固体颗粒分离效率也相对较低。在添加20%柴油时,脱渣率仅为68.1%。
由斯克托斯定律可知,大颗粒具有较高的沉降速度,在一定的时间内,可以沉降于底部的小固体颗粒粒径为该工况下的临界分离粒径。油泥掺轻质油沉降分离临界分离粒径变化显示,3种轻质油临界分离粒径变化规律与表2黏度变化趋势一致,说明油泥黏度是决定一级分离效率的关键因素。当添加5%、10%、20%煤油时,临界分离粒径分别为158.4、61.2、15.1μm。而添加甲苯时,可分离颗粒粒径略大于添加等量煤油时粒径。综合考虑,将选用煤油作为调质轻质油。在工程应用中,可根据油泥的颗粒粒径分布,二级分离系统入口油泥含固率要求及固体颗粒粒径要求,调整轻质油添加比例。
2.2 二级分离系统工艺优化
油泥中水以分散的乳化液滴形式稳定分布于油相,二级分离的主要目的是利用微乳液对油水混合物破乳,并通过离心分离脱水、脱渣。
2.2.1 微乳液配方选择及优化
微乳液体系具有超低界面张力,约为10-6~10-7N/m,具有很强的润湿、分散和增溶能力。在一定范围内,微乳液既能与水又能与油混溶,可消除油水间的界面张力,从而破乳。为了筛选破乳油泥的较优配方,以不同油相、助乳化剂、水油比配制了一系列微乳液,对其脱水效果进行了对比研究,结果见表4。
表4:微乳液配方对油泥脱水率的影响
序号 | 油 | 助乳化剂 | 水油比 | 脱水率/% |
1 | 甲苯 | 异丙醇 | 1:1 | 53.2 |
2 | 甲苯 | 正丁醇 | 1:1 | 66.5 |
3 | 甲苯 | 乙醇 | 1:1 | 56.6 |
4 | 煤油 | 异丙醇 | 1:1 | 69.2 |
5 | 煤油 | 正丁醇 | 1:1 | 78.2 |
6 | 煤油 | 乙醇 | 1:1 | 82.7 |
7 | 煤油 | 乙醇 | 4:1 | 81.1 |
8 | 煤油 | 乙醇 | 3:1 | 90.5 |
9 | 煤油 | 乙醇 | 2:1 | 78.5 |
10 | 煤油 | 乙醇 | 1:2 | 64.8 |
11 | 煤油 | 乙醇 | 1:3 | 87.5 |
12 | 煤油 | 乙醇 | 1:4 | 83.5 |
在相同水油比、相同种类助乳化剂配方中,油相为煤油的微乳液比为柴油的微乳液破乳脱水效果好。在相同油相、相同水油比配方中,助乳化剂为乙醇和正丁醇的微乳液脱水效率高。通过不同水油比配方筛选,确定煤油、乙醇、水油比3:1的微乳液配方为油泥二级分离系统破乳剂。
2.2.2 微乳液添加量对脱水率影响
在保证破乳脱水效率的情况下,应尽可能的降低微乳液的使用量。将等量的油水混合物中分别添加0%、3%、5%、7%、10%的微乳液,以脱水率为主要评价标准,确定油泥中微乳液的添加量。随着微乳液添加量的逐渐增加,油泥脱水率不断提高,且脱水率变化速率趋缓。当不添加微乳液时,在给定的离心条件下,脱水率仅为10.1%。当添加3%微乳液时,离心后油泥含水率急剧下降,比未添加微乳液时脱水率提高了51.2%。当添加量增至5%时,油泥脱水率可提高到90.5%。当调质微乳液加入量为7%和10%,脱水率变化不大,分别为95.3%和96.1%。实验中观察得知,在添加10%微乳液时,微乳液未能完全与油泥混溶,一部分微乳液浮于表面造成浪费。而添加7%时,油泥可很好地与微乳液混溶,微乳液可较大限度地发挥分散、增溶、破乳效果。从经济性和处理效果两方面考虑,确定7%为较佳添加量。
2.2.3 含油污泥两级分离工况组合及产物分析
通过一级分离工艺优化,确定煤油为较佳掺混轻质油。在二级破乳脱水实验中,确定了较优微乳液配方和添加量。在煤油不同添加量及是否添加微乳液工况组合下,对含油污泥两级分离系统分离效率及产物成分进行了分析。不同工况组合下两级分离系统对乳化水、固体渣的临界分离粒径见表5。
表5:不同工况下油泥水、渣临界分离粒径
工况 | Ⅰ | Ⅱ | Ⅲ | Ⅳ | Ⅴ | Ⅵ |
煤油添加量/% | 5 | 5 | 10 | 10 | 20 | 20 |
微乳液添加量/% | 0 | 7 | 0 | 7 | 0 | 7 |
临界分离水粒径/μm | 6.8 | 3.6 | 6.3 | 3.1 | 5.3 | 2.6 |
临界分离渣粒径/μm | 31.5 | 26.9 | 15.1 | 11.5 | 7.5 | 6.6 |
由表5可知,固体渣的脱除主要取决于一级分离系统煤油的掺混量,二级分离中,微乳液的添加可进一步降低油泥粘度,固体渣的临界分离粒径进一步减小。在煤油添加量20%,微乳液添加7%工况下,可将油泥中大于6.6μm的颗粒脱除。乳化水的脱除主要依靠微乳液破乳实现,在20%煤油添加量下,不经微乳液调质无法分离粒径小于5μm的乳化水滴,而添加7%微乳液后,可实现2.6μm以上粒径的水滴被脱除。在表5的6种工况组合下,分离得到的回收油成分结果显示,在20%煤油、7%微乳液添加工况下,可实现回收油含油量大于95%,回收油中水及固体渣的总含量小于3%。
3 结论
(1)针对含油污泥成分组成和分离特性的不同,设计了基于调质-离心的油泥2级分离处理系统,并提出了适用于不同油泥的具体处理方案。与传统油泥处理技术相比,该分离系统具有适用范围广、油回收效率高、回收油品质高的优势。
(2)在工艺优化实验中, 应该DSC技术表征油泥中乳化水粒径分布变化,分析了不同工况条件下油泥中固体渣、乳化水的临界分离粒径,可用于预估不同油泥在两级分离系统中的分离效果,为工业化应用提供重要的数据支持。
(3)通过一级分离工艺优化实验,得出煤油具有较佳的降黏脱渣效果,在添加20%煤油时,粒径在15.1μm以上的渣可以被脱除。同时,掺混轻质油可提高回收油的油品,提高油泥的流动性,减少处理过程中管道运输成本,实现节能降耗综合利用的目标。
(4)通过微乳液这一新型药剂的调质,可大大提高油水分离效果,克服了油泥离心脱水处理效果不稳定的缺点。可将油泥中乳化水的临界分离粒径降至3μm以下。