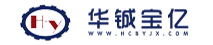
1 油田含油污泥主要来源及特点
目前,大庆油田产生的含油污泥主要来自两个方面:一是,在集输处理过程中沉积在各类容器、大罐和回收水池等地面设施中,定期清理产生的污泥;这类容器设施一般包括:污水沉降罐、除油罐、油罐、二合一加热炉、游离水分离器、加热炉、电脱水器、回收水池等;二是,油井作业、集输油管道腐蚀穿孔等产生的落地污泥。仅杏北油田,目前,每年约产生含油污泥15000m³,其中容器清淤污泥约占总污泥量的85%。
由于油田含油污泥来源广泛,污泥的组分也非常复杂,一般含有大量老化油、蜡质、沥青质、胶体、固体悬浮物、细菌、盐类等,还包括生产过程中投加的各种药剂,有些含油污泥中还夹杂有滤料、垢质、石块等杂质。通过对不同来源污泥的分析显示,油田产生的含油污泥含油在15%~70%,含固体悬浮物在10%~60%,其特点是含油、含固体悬浮物高且很不稳定,杂质多,处理难度大。
2 调质-离心处理工艺
杏北油田含油污泥处理站2009年投产,设计处理规模10t/h,设计指标为处理后污泥含油≤2%。主工艺采用调质-离心处理工艺,整个处理站主要由污泥流化预处理装置、调质装置、离心装置、油水分离装置、回掺水装置、导热油加热装置等部分组成。
2.1 污泥流化预处理
污泥流化预处理装置主要由进料斗、转鼓分离器、曝气沉沙池及大颗粒提升装置组成。其主要功能是去除污泥大粒径颗粒,改变污泥流动状态。首先,污泥通过料斗格栅进入料斗去除>200mm固体颗粒;再通过转鼓分离器,通过热水喷淋和旋转分离去除>20mm的固体颗粒,同时稀释污泥;然后通过曝气沉砂装置去除>5mm的固体颗粒,实现污泥的流化。该装置处理后的污泥温度可超过45℃,固体颗粒粒径≤5mm。
2.2 污泥调质装置
主要设备为调质罐,其作用是对流化污泥进一步加热、搅拌、匀化。同时,加入清洗剂、调节剂和破乳剂,以提高调质效果,使油、泥充分分离,油、水充分破乳。通过静止沉降,使油、水、泥分层,上层污油溢流回收,下层污水和污泥进入离心机处理。
2.3 污泥离心装置
该部分是污泥处理的核心部分,主要设备为离心机。调质后的含油污泥通过离心机的高速旋转进行固液分离。分离出的固体(含油率低于2%,含水可达30%~40%)输送到污泥堆放场,分离出的液体进入油水分离装置进一步分离。离心过程加入絮凝剂,提高固液分离效果。
2.4 油水分离装置
油水分离装置主要设备为卧式容器,具有沉降、分离、缓冲功能,主要是对溢流出的污油及离心出的液体进行油水分离,将分离出的油回收,分离出的水作为回掺水循环利用。
2.5 回掺水装置
主要由回掺水罐及回掺水泵组成,功能是将回收的污水加热并供给整个污泥处理系统循环使用。
2.6 导热油加热装置
由导热炉及相关导热管线组成,通过加热炉加热导热油,为预处理装置的曝气沉沙池、调质罐、油水分离器、回掺水管伴热,为整个系统提供热能。
3 工艺运行参数优化
由于该处理工艺 在大庆油田使用,为了使系统能够达到相应的处理指标并稳定运行,因此,需要对系统各装置的运行参数进行研究和摸索。
3.1 污泥流化预处理装置
回掺水的作用是加热稀释并冲洗污泥,将大颗粒物料冲洗干净,分离出去。要求满足的指标:分离出的大固体物料含油≤5%;稀释后的污泥温度超过45℃。
目前,污泥处理站采用人工卸泥的方式进料,进料速度约10m³/h,按此进料速度对预处理装置的回掺水温度和水量进行试验。
经过试验研究,当回掺水温度超过75℃,回掺水量超过25m³/h时,可满足指标要求,经过预处理后的污泥含固量一般低于15%,含油一般在5%~25%。
3.2 污泥调质装置
流化污泥进入调质罐后,需要对污泥进行加药,升温,搅拌,沉降以达到较佳的调质效果,即实现油、水、泥的充分分离。
3.2.1 污泥调质温度优化
针对性质相同的含油污泥,经过相同的调质时间和沉降时间,进行不同的调质温度试验研究。试验研究表明:无论初始的污泥含油如何,调质温度越高,调质后的污泥含油率越低,当调质温度超过60℃后,调质效果基本趋于稳定。因此,从节约能耗的角度考虑,系统较佳的调质温度为60℃。
3.2.2 调质药剂优化
一是,清洗剂可以降低油/水、油/泥的界面张力,便于油、泥的充分分离。针对相同来源的含油污泥,在其他参数相同的条件下,加入不同剂量的清洗剂,以清洗后的污泥含油率为指标优化清洗剂的投加量。通过5个含油范围的来泥试验得出:来泥的含油量越高,所需的清洗剂也越多。各种含油级别的污泥所对应的较佳的清洗剂投加量见表1。
表1:不同含油污泥所对应的清洗剂投加量
流化后污泥含油/% | 5 | 10 | 15 | 20 | 25 |
清洗剂用量/(mg/L) | 500 | 750 | 1000 | 1250 | 1500 |
二是,破乳剂的加入可提高油、水分离效果,利于污油溢流回收,提高污泥离心效果。针对相同来源的含油污泥,在其他参数相同的条件下,加入不同量的破乳剂,以调质沉降后的上层污油含水率为指标优化破乳剂的投加量。试验得出不同含油范围的污泥所对应的破乳剂投加量见表2。
表2:不同含油污泥对破乳剂投加量
流化后污泥含油/% | 5 | 10 | 15 | 20 | 25 |
破乳剂加药量/(mg/L) | 750 | 1000 | 1250 | 1500 | 1750 |
3.3 污泥离心
离心装置是固液分离的关键,其效果好坏主要取决于离心机的转数及转数差。
3.3.1 离心机转数优化
针对同一调质罐内的污泥,调整离心机转数,观察出泥油含量变化情况。试验证明:离心机转速在2700~3200r/min,转数越高离心效果越好,当转数超过2900r/min后效果趋于稳定。而离心机的转数越高,轴瓦温度也增高,影响离心机的安全运行。因此,离心机的转数应该根据轴瓦的实际温度在2900~3100r/min进行调整,且不应低于2800r/min。
3.3.2 离心机转数差优化
针对同一调质罐来泥,将离心机的转数设定在2900r/min不变,调整离心机的转数差(3~8r/min),观察处理后污泥含油、含水率的变化。试验得出,随着转数差的降低,污泥含油和含水率越低,但是,转数差过低易造成离心机出泥缓慢甚至堵塞。结合现场实际,离心机转数差约在5r/min时,既可保证处理效果,又能保证离心机稳定运行。
3.3.3 絮凝剂
絮凝剂可与水中微粒起电荷中和及吸附架桥作用,有利于固、液分离。针对同一调质罐内的污泥,在离心机参数不变的情况下,加入不同剂量的絮凝剂,以处理后的污泥油含量为标准优化絮凝剂的投加量。试验表明在保证出泥效果的前提下,随着污泥固体含量的增加,所需的絮凝剂的量也增加,过少或过多的絮凝剂均会影响出泥效果。
3.4 油水分离器
油水分离器具有缓冲、沉降、分离的作用。油水分离装置的工作原理是依靠油、水的重力沉降作用,利用罐内的隔板,将沉降后的上层污油回收,下层的污水通过泵打入回掺水罐供系统循环利用。
为了控制回掺水中的污油,保证回掺水的质量,需要对油水分离器的沉降时间进行优化。试验得出油水分离器的沉降时间应不低于4h。
通过各单体的参数优化试验,得出了不同来泥情况下所对应的操作参数。按照得出的运行参数,随机进行了实际处理效果的检验。处理后的污泥平均油含量达到了1.48%,均小于2%,说明在优化出的参数下运行可以保证污泥处理的效果。
4 运行成本及经济效益分析
4.1 运行成本
该套处理工艺在杏北油田已运行4年,使用成本主要包括天然气、药剂、耗电、耗水以及设备维护成本,投产初期由于运行参数不明确,污泥处理成本达到312.8元/m³,优化参数后的运行成本仅为154.7元/m³。
4.2 经济及社会效益
杏北油田含油污泥处理站自2009年投产以来累计回收原油6850m³,原油密度按照0.8602g/cm³计算,累计回收原油5892.37t。原油价格按2382元/t计算,累计创经济效益1403.56万元。
5 结语
含油污泥调质-离心处理技术的成功应用,使杏北油田的含油污泥得到了有效的减量化、资源化处理,大大降低了含油污泥对环境的污染,具有较好的经济效益和显著的社会效益。该技术目前已在大庆油田多个采油厂推广应用,成为大庆油田含油污泥处理的主要手段,为绿色油田的发展建设提供了技术支持。