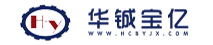
“三泥”是炼油厂污水净化工艺过程中产生的油、水、渣混合物,其主要来源于隔油池池底沉积的油泥;浮水池投加絮凝剂后空气浮选时产生的浮渣;曝气生化单元的剩余活性污泥。由于“三泥”可使周边土壤毒化,对周边水体形成污染,同时“三泥”中含有相当可观的污油,因此,从回收资源、降耗增效方面和减少排污、保护环境方面考虑,完善和严格的污泥处理工艺是必要的。
国内外炼油厂先后建立了污泥调质-脱水-焚烧的处理工艺,这一工艺对活性污泥、油泥和浮渣有较好的处理效果,但存在两个主要问题:一是污泥调质后,经重力沉降形成浮渣-污水-泥三相,这时的污水相悬浮物和油含量较少,与泥相和渣相同时进行机械脱水实际上增加了离心相的负荷;二是在调质后的污泥机械脱水分成泥-水-油三相,其中水相的悬浮物和COD含量较高,同时含油2%左右,无法直接排放。这两部分水相中所含的油有相当一部分是乳化油,采用传统的方法不易处理,而膜分离这一新型的技术在油水分离,特别是乳化油和水的分离方面有独特的优势。
1 实验
1.1 实验材料
本实验所用“三泥”为扬子炼油厂提供,其中除油、水、渣等物质外,还有“三泥”预处理过程中添加的絮凝剂聚合铝成分。“三泥”静置48h以上,经自然沉降有明显分层,自上而下为浮渣、水、泥三层。取水层作为实验对象,水层的油含量为6g/L。
本实验采用南京化工大学膜科学技术研究所研制的0.2μm和1.0μm氧化锆陶瓷膜。膜厚为20~30μm,孔隙率为30%,膜管长为20cm。
1.2 实验方法
实验装置前文已有报道,原料液油含量采用重量法测定,渗透液油含量采用紫外分光光度法测定。
2 结果与讨论
2.1 膜孔径的选择
膜过滤主要通过对油滴和悬浮粒子的有效截留实现油水分离,选择膜孔径的一般标准是保证一定截留率的情况下获得较高的渗透通量。1.0μm的膜由于孔径较大,过滤初期膜孔的阻塞较严重,所以膜通量下降较快,而孔径较小的0.2μm的膜通量衰减相对较小。两种膜的稳定通量基本相同。
表1 是过滤趋于稳定时渗透液的油含量值。从表中可以看出,通过陶瓷膜过滤,料液的油含量有明显降低,其中1.0μm的膜由于孔径较大,小油滴容易透过膜孔进入渗透液,对油的截留率相对较低。从通量和截留率的测定结果,选用0.2μm的陶瓷膜较合适。
表1:膜孔径与透过液性质的关系
膜孔径 | 油含量/(mg/L) | 截留率/% |
0.2μm | 30.0 | 99.5 |
1.0μm | 296 | 95.1 |
2.2 膜过滤性能随时间的变化
在过滤的起始几分钟通量下降较快,然后下降趋势逐渐减缓,约在40min以后基本稳定。这说明在过滤的过程中,随着过滤时间的增加,膜孔及表面逐渐被污染,与Belfort等人的研究结果一致。
对于本文研究的油水体系,过滤开始的通量下降是由于油滴在膜表面和孔内的吸附引起的,随着过滤的进行,一定量的油滴在膜表面形成对过滤分离有影响的拟稳定吸附沉积层,所以通量趋于稳定。
表2为不同过滤时间取样的渗透液油含量的分析结果,从表中可以看出,截留率随过滤时间的增加而不断提高,30min后趋于稳定。
表2:截留率随时间的变化
时间/min | 渗透液油含量/(mg/L) | 截留率/% |
5 | 65.5 | 98.9 |
30 | 41.2 | 99.3 |
120 | 30 | 99.5 |
2.3 操作压力的影响
压力是膜过滤时的传质推动力,也是影响膜过滤性能的重要因素之一。压差≤0.135MPa时,膜的初始通量和拟稳定通量随压力升高而增加;压差>0.135MPa时,初始通量和拟稳定通量随压力升高变化很小。
这是由于操作压差升高虽然增加了过滤推动力,但同时也增加了污染的可能性。因此压差>0.135MPa时,膜的拟稳定通量随压力升高几乎不变。但初始通量随压力升高几乎不变的现象在已有的报道中很少。对于本实验体系,出现这一现象可能是随着压力的升高,吸附和浓差极化引起的通量迅速下降段的时间很短,在手动操作的实验装置上,这段下降段不易测定,所以在高压下测定的初始通量已接近沉积层过滤阶段,从而出现初始通量随压力几乎不变的情况。
对于“三泥”的水相,同样存在一个临界压力——0.135MPa。超过临界压力后,操作压差增大,通量随压力的变化明显减小。这说明,此时推动力和阻力的增长基本持平,工业操作应选取略小于临界压力的值。
2.4 膜面流速的影响
在陶瓷膜过滤液体的应用中,一般采用错流过滤的方式,以减少膜表面的沉积和浓差极化的影响。一般文献认为膜面速度越大,膜通量越高,但是膜面速度的提高意味着能耗的增加;同时对有些体系,膜面流速的增加还会造成渗透通量的下降,因此研究膜面速度对过滤性能的影响很有必要。
在不同膜面速度下,通量随时间而衰减。流速增大,膜通量随时间衰减的幅度减小。这是由于流速增大,膜管内流体的剪切力随之增大,带走膜面的颗粒(或渣)就越多,因而减少了滤饼层的厚度,减小了过滤的阻力,同时也减小了浓差极化的影响。
流速越高,通量越大,但升高的幅度逐渐减小。流速小于1.17m/s时,流速对通量的影响较为显著,当流速高于1.17m/s后,随流速的增大,通量增长的幅度降低。这说明含油体系的流型在1m/s左右有显著的变化,通过计算不同流速所对应的雷诺数Re(见表3)证实了这一点。流速从0.58m/s变化到1.17m/s的过程中,流型是从过渡区发展到湍流区,因此流速对膜通量的影响很明显;而流速大于1.17m/s后,流动进入湍流区,无流型的变化,所以流速对通量的影响减小,但随流速增大,拟稳定通量基本呈线性增长。较佳流速需根据对产量的要求和所配置的泵来确定。
表3:不同操作流速对应的雷诺数
流速/(m/s) | 0.58 | 1.17 | 1.75 | 2.34 |
Re | 4608 | 9295 | 13902 | 18590 |
2.5 操作温度的影响
温度对过滤过程的影响比较复杂。温度上升,料液的粘度下降,扩散系数增加,减小了浓差极化的影响;但温度上升又会使料液的某些性质改变,从而改变料液对膜的污染程度。Villaroel Lopez等对含油废水的实验结果认为:温度升高,可以减小料液的粘度,从而可以提高通量,但温度对油滴的粒径分布亦有影响,可以使粒径减小,从而使通量降低,因而存在一个操作的较佳温度。
表4:操作温度与拟稳定通量的关系
温度/℃ | 30 | 40 | 50 |
渗透通量/(L/m²·h) | 235.0 | 340.9 | 328.9 |
表4为操作压差0.10MPa,膜面速度1.75m/s时,不同温度下拟稳定通量的数值。由表中可看出:对于本实验体系,较佳操作温度为40℃,温度对渗透通量的影响与Villaroel Lopez等的研究结果一致。
3 结论
(1)采用陶瓷膜处理“三泥”水相能明显地降低水相的油含量,为炼油厂“三泥”无害化处理开辟了一条新途径。
(2)膜过滤过程中膜通量开始迅速下降,40min后基本达到稳定,截留率在30min后趋于稳定,合适的膜孔径为0.2μm。
(3)实验确定0.135MPa为临界压力。流速小于1.17m/s时,流速的提高可导致渗透通量的明显增加,当流速高于1.17m/s时,流速对通量的影响减小,实际操作应在湍流区进行。温度对膜通量的影响较为复杂,本体系的较佳操作温度为40℃。