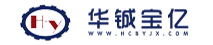
随着工业化的迅速发展,油品的使用量越来越大,但由于各种技术的限制和管理落后等原因,大量油品进入水体,形成污染。含油废水的来源很多,石油工业的采油、炼油、贮油运输及化工工业都会产生含油废水,油轮压舱水、洗舱水、机械工业的冷润滑液、轧钢水,及食品工业等的废水中也都含有大量的油品。
油在水中的存在状态大体可以分为浮油、分散油、乳化油。含油废水主要含有浮油,占总含油量的70%~80%。浮油的油粒粒径较大,一般大于150μm,它的去除相对较为容易:分散油以油粒的形式分散在水中,粒径在25~150μm之间,不稳定,静置一段时间后往往变成浮油;乳化油在废水中呈乳浊液,水中有表面活性剂使乳化油处于稳定状态,油粒一般小于20μm,油粒间难以合并,难以分离。进入水体,危害水产资源和人类健康。为保护环境不受污染,并能回收一些有用物质,对含油废水必须进行处理。各种工业膜分离法的分类及其应用列于表1。
表1:工业膜分离法
分离膜 | 分离机制 | 分离膜孔径 | 应用 |
微滤 | 过滤 | 多孔,孔径0.1~10μm | 细胞收集,液体滤清,减少细菌和粒子,水精加工等 |
超滤 | 过滤 | 1~100μm | 牛奶加工,果汁滤清,油水分离,生物分子分离,胶态硅石清除,UHP精加工 |
毫微滤 | 吸附-过滤 | 2nm | 水软化,色素,染料和低分子化合物清除 |
反渗透 | 选择性吸附毛细管流动 | 1nm | 水脱盐,UHP水预处理,废水处理,食品加工 |
渗透蒸发 | 溶解-扩散 | 非微孔薄膜 | 共沸混合物分离 |
1 含油废水的处理方法
含油废水处理技术按其作用原理和去除对象一般可分为物理化学法(主要有气浮法、膜分离法、吸附法、粗粒化法等)、化学法(主要有化学絮凝法、化学氧化法、电化学法等)和生物处理法(主要有活性污泥和生物滤池法)等。各种单一净化方法都有其局限性。膜分离技术在近几年得到了广泛的应用,尤其是有机高分子膜的应用,取得了令人瞩目的发展。
2 膜法处理含油废水
膜分离法是在近20年迅速发展起来的新型分离技术。传统的含乳化油废水的处理方法常辅以电解、絮凝等先行破乳过程,能耗和物耗较大。而膜法处理含乳化油废水,一般可不经过破乳过程,直接实现油水分离。并且在膜法分离油水过程中,不产生含油污泥,浓缩液可焚烧处理;处理量和水质较稳定,不随进水中油浓度波动而变化;一般只需压力循环水泵,设备费用和运输费用低,特别适合于高浓度乳化油废水的处理。膜分离除油,关键在于膜的选择。目前用于油水分离的膜通常是反渗透、超滤和微滤膜,它们的作用是截留乳化油和溶解油。简单的情况是乳化油基于油滴尺寸被膜阻止,而溶解油的被阻止则是基于膜和溶质的分子间的相互作用,膜的亲水性越强,阻止游离油透过的能力越强,水通量越高。
2.1 微滤
微滤技术是目前所有膜技术应用较广泛的一种膜分离技术。微滤主要用于过滤0.1-10μm大小的颗粒、细菌、胶体。其过滤原理和普通过滤相似,属于筛网过滤。微滤过滤具有操作压力低(<0.2MPa),对水质的适用性强、占地面积小的优点。微滤时过滤方式有死端过滤和全量过滤两种方式。
陶瓷微滤摸的主要特点是具有催化性、化学稳定性和热稳定性,使用寿命长。韩国的Lee Shihee等用α-Al为活性层、平均孔径为0.4μm的陶瓷膜对油粒粒径为11μm的乳化油进行处理,实验结果表明:错流速度越大膜通量越大。实验得出的较优操作条件是错流速度2m/s,每过滤5min反冲洗4s,在这种条件下操作可以使膜通量稳定在135L/(m2·h)。在膜清洗时,分别用硝酸、氢氧化钠、丙酮、甲苯等溶液在相同的操作压力100kPa、错流速度0.5m/s的条件下,对被污染的膜清洗5min,结果表明甲苯的清洗效果较好,可使膜通量恢复到84%。胜利油田PP中空纤维辩滤膜处理含油污水,原水悬浮固体质量浓度<3mg/L,经该微滤元件过滤后,悬浮固体质量浓度≤1mg/L,粒径≤1μum,含油质量浓度≤1mg/L,符合低渗透、特低渗透油田的注水标准。
2.2 超滤
超滤膜也属于压力驱动膜,其分离原理一般认为是筛分过程。其孔径范围为0.05~1nm。它用于分离可溶性聚合物、生物分子、分散体和胶体,因大溶质渗透压很低,操作的压力较低,一般为0.07~0.7MPa。此外,因超滤膜表皮中的孔大于反渗透膜中的孔,超滤的通量比反渗透膜的通量大一个数量级。超滤膜分离与膜的孔径、溶质-膜的相互作用和大分子的形状和粒径有关。为获得较大分离效果,待分离的各物质的粒径应相差10倍。此外,因所有膜都有一定的孔径分布,膜相对分子质量截分率至少为待清除的较小溶质的截分率的1/2。
超滤过程是一种无相变的,非破坏性的分离过程。经超滤膜处理后的含油废水浓缩液中油的质量分数高达50%。浓缩液可以通过离心分离法进一步分离。收集的油不能回用,但是可以通过焚烧以减少污染。超滤膜对含油废水的处理效果与含油废水的性质相关。
美国Abgor.inc.公司生产的超滤膜在处理芝加哥Dewey&Almy的含油废水中取得成功。处理前的油含量为3.5g/L左右,处理后透过液中含油降为35mg/L,并可同时降低水中生物耗氧量(BDO)、化学耗氧量(COD)值,试验中采用管式HDF膜,膜孔径小于0.005m,膜面积72.1m2,平均膜通量为71.1m3/d,装置正常运行3年。由于膜本身及密封圈受温度的限制,不能在较高温度下操作,一般在30~50℃之间。韩国Changa等的研究表明,超滤膜在处理铅、铁清洗液含油废水时,处理效果并不理想,COD的去除率分别为1.3%和9.9%。总有机碳(TOC)的去除率分别为2.2%和10.3%;而对切削加工过程产生的含油废水的处理效果较好,COD和TOC的去除率分别达到93.2%和93.5%。这一现象可以解释为清洗液废水中含有的主要是相对分子质量在200~400之间的表面活性剂,而超滤膜的截流平均相对分子质量为30000,超滤膜对表面活性剂这样的小分子物质几乎没有去除作用。唐燕辉等利用自行设计、组装的膜处理装置,考察了多种制膜方式,实验表明用加压制膜法制备的超滤膜,分离机械加工排放的含油污水时,可以使CODcr从728.64mg/L降至87.8mg/L,含油质量浓度从5000mg/L降至2.5mg/L,脱除率分别达到87.95%和99.95%,分离后排水已达到 规定的排放标准。船舶机舱废水的水量虽然不大,但含油量高达10%~20%,对这种废水首先采用重力分离法,去除绝大部分浮油,使废水含油量降为100mg/L,然后进入超滤器除油,使出水含油量在10mg/L以下,超滤器的操作压力≤2.45×105Pa,水通量为60L/(m2·h),设备处理能力为0.2~1.0m3/(h·台)。张裕媛等用相转化法制备聚砜-Al2O3微粒填充到聚枫中,并用该复合膜对华北油田北大站外排水沙滤后水样进行了超滤处理,原水的油质量浓度为640mg/L,处理后的油田浓度小于0.5mg/L,完全符合回注水的要求。
2.3 反渗透
反渗透是用于从溶液中清除溶解的离子之类的溶质的一种分离法。反渗透膜的孔径<1nm,水分子(半径0.1nm)能自由的通过这些孔,但溶解的离子和有机溶质不能。这些溶质或是被膜表面截留或是被水相的比膜表面更强的吸附作用吸引。由于膜、溶质和溶剂间的相互作用,水分子选择性吸附于溶剂-膜的界面使分离得以实验。和非微孔的气体分离膜和渗透蒸发膜不同,反渗透膜的表面层具有双峰孔径分布,小孔(≤1nm)和偶尔存在的大孔(≥10nm)造成表皮层中不可免的缺陷。有时,反渗透膜有针孔和其他导致截留率降低的缺陷。反渗透膜很容易被污染,导致废水处理效果和膜通量下降。因此进入反渗透装置的废水一般都要经过预处理,达到一定的指标以后才可进入。
Krakulski等将超滤与反渗透(UF-RO)联合应用于含油废水的处理工艺中,实验检测结果表明:用单一的超滤膜处理未经任何处理的含油废水,透过液中的油质量浓度低于10mg/L,COD的去除率可达80%;用超滤-反渗透工艺处理同种含油废水,COD的去除率可提高到98.5%,溶解性总固体(TDS)去除率可达到95.7%,用超滤-反渗透工艺处理含油废水时出水中的含油量几乎为零,可作为工业回用水。
3 结语
近年来,膜法处理含油废水技术发展很快,新型膜特别是功能高分子有机膜的研制与开发使膜法处理含油废水技术趋于成熟。膜分离技术用于废水处理具有能耗低、效率高和工艺简单等特点。膜组件简洁、紧凑、易于自动化操作、维修方便,与其他废水处理方法相比具有明显的优势,所以在废水处理中已受到特别的青睐。但膜分离自身有一些缺点:如热稳定性差、不耐腐蚀、膜易被污染等。我们应该清晰的认识到,单一的膜分离技术并不能很好地解决含油废水的处理问题,要把多种膜分离技术同传统的气浮、盐析、混凝和粗粒化等方法结合在一起,在不断解决膜污染、膜清洗、膜通量及降低膜分离处理成本的前提下,开发新的工艺、新型膜组件和新型膜,只有这样才能更好的处理含油废水。