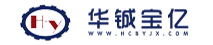
随着吉林油田扶余采油厂热采、调剖等采油工艺技术的应用,采出液性质发生变化。导致联合站脱水系统沉降罐内形成的老化油加厚。老化油的破乳脱水极为困难,它会随着分离后的净化油、污水等进入其他处理环节,严重破坏油水分离过程,影响原油脱水质量和含油污水处理效果,威胁到采出液和含油污水处理设施的正常运行。对老化油进行回收再处理,不仅可以使其达到净化油标准出厂销售,同时还可以保障脱水系统的正常运行操作,兼具环境与经济效益。
1 老化油组成
1.1 实验方法
老化油与净化油(脱水原油)样品均取自扶余油田中心处理站,采样日期分别为2009年的1月(1#样品)、3月(2#样品)、4月(2#样品);净化油采样日期为2009年3月。样品含水率分析主要采用GB/T260-88《石油产品水分测定法》,SH/T0509-1992《石油沥青组分测定法》。样品水相分析主要是Fe2+、S2-等指标,样品固相分析主要为FeS以及机械杂质含量。
1.2 老化油与净化油含水率分析
样品进行实验室测定。老化油1#样品含水率为46.8%,2#样品68.9%,3#样品70.9%,而净化油为1.6%。含水率分析表明,与净化油相比,老化油不仅含水率较高(平均62.2%),而且含水率波动较大(在46.8%~70.9%之间)。低温破乳或静置会导致游离水析出,但大部分水仍然与油乳化较好。
1.3 老化油与净化油的四组分分析
净化油沥青质含量0.32%,老化油平均为0.65%,老化油的沥青质含量较高。老化油胶质含量平均为8.80%,略低于净化油的9.16%。老化油与净化油在沥青质与胶质含量上相差不大。老化油与净化油四组分含量分析结果见表1。
表1:老化油与净化油四组分含量(%)
分析指标 | 1#老化油 | 2#老化油 | 3#老化油 | 净化油 |
沥青质 | 0.64 | 0.68 | 0.62 | 0.32 |
胶质 | 8.70 | 9.23 | 8.48 | 9.16 |
芳香化合物 | 15.65 | 16.61 | 15.25 | 15.77 |
饱和烃 | 49.02 | 52.03 | 47.76 | 51.92 |
1.4 老化油与净化油的固相含量分析
将老化油样品中分离出的黑色固体颗粒用水配制成分散体系,然后用库尔特粒度仪进行粒径分布分析。黑色固体颗粒通过高速离心机分离后烘干,研磨后用X射线衍射仪对其晶体结构进行测定,确定为FeS。老化油与净化油的FeS与不溶固体含量,以及FeS粒径分布见表2。
表2:老化油与净化油固相含量分析结果
分析指标 | 1#老化油 | 2#老化油 | 3#老化油 | 净化油 |
FeS含量(mg/L) | 502 | 491 | 511 | 未检出 |
FeS粒径分布(μm) | 3.66~66.68 | 4.35~70.46 | 5.12~67.42 | 未检出 |
不溶固体含量(mg/L) | 51 | 63 | 55 | / |
与净化油相比,扶余油田老化油中含有大量的FeS颗粒与机械杂质,FeS含量平均高达501.33mg/L,不溶固体杂质平均56.33mg/L。FeS作为界面活性物质,有助于油水乳化,促进油-水中间过渡层生成。老化油中FeS粒径分布为3.66~70.46μm,呈胶体状态,因而活性更强。
1.5 老化油水相组成分析
老化油水相的组成也是老化油组成的重要部分,其中Fe2+、S2-等指标对于推测老化油形成机理具有重要意义。老化油中含有较多的Fe2+、S2-,可见这两种离子对老化油的形成贡献较大,初步判断其为老化油形成的主要原因。
老化油水相离子浓度分析结果见表3。
表3:老化油水相组成分析结果(mg/L)
分析指标 | 1#老化油 | 2#老化油 | 3#老化油 | 净化油 |
Ca2+ | 839 | 812 | 1012 | 825 |
Mg2+ | 101 | 86 | 132 | 127 |
Na+ | 21100 | 20100 | 24600 | 22300 |
HCO3- | 64 | 87 | 52 | 56 |
Cl- | 10139 | 12645 | 15023 | 11500 |
SO42- | 12 | 26 | 17 | 13 |
Fe2+ | 185 | 174 | 199 | 36 |
S2- | 182 | 157 | 209 | 28 |
老化油与净化油水相中的Ca2+、Mg2+、Na+、Cl-、HCO3-、SO42-指标比较接近;但对于关键指标Fe2+,净化油水相含量仅为36mg/L,而老化油水相Fe2+含量高达174~199mg/L;净化油水相中S2-含量仅为28mg/L,而老化油水相S2-含量高达157~209mg/L。
2 老化油产生的机理研究
通常认为:采出液处理工艺、天然活性组分是油-水中间过渡层形成的原因。硫酸盐还原菌(SRB)腐蚀管道生成FeS,FeS富集在油水过渡层中,也会使中间层不断加厚形成老化油。对于扶余油田的老化油的产生机理还要具体分析。
2.1 胶质、沥青质乳化机理
原油中的胶质、沥青质等带有强极性基团,表面活性高,吸附在油水界面,可形成高弹性的界面膜,胶质、沥青质含量越高,油水界面膜强度越高,乳状液也越稳定。在稠油油田,胶质、沥青质等强极性组分被认为是造成油水乳化的主要原因。然而分析扶余油田老化油与净化油的胶质、沥青质含量可知,沥青质含量较低,胶质含量相差不大,说明胶质、沥青质并不是形成老化油的主要原因。
2.2 硫化亚铁乳化机理
以1#老化油样品为例,FeS粒度分布在3.661~66.68μm之间,平均为5.813μm,其他老化油样品中FeS粒度分布也很相似。FeS颗粒呈胶态,是乳状液的良好稳定剂。利用SY/T0532-1993《油田注入水细菌分析方法绝迹稀释法》,老化油中检测到SRB,老化油的产生与SRB新陈代谢过程有关,SRB以菌落形态附着在设备与管道内壁,其大量繁殖会给金属材料带来严重腐蚀,同时产生黑色FeS沉积,富集在脱水器的油水过渡层中,起到稳定乳化液的作用。胶态FeS颗粒对油-水中间过渡层的稳定机理是堆积在油水界面上,形成紧密排列的刚性界面膜,阻止水滴之间聚结,促进老化油形成。
2.3 硫化亚铁乳化机理的验证
采用溶剂分离-离心法从扶余油田老化油中分离出胶态FeS颗粒,将其与取自扶余油田的净化油、新鲜水混合,配制成含水率为70.0%的原油乳状液,在80℃条件下振荡6h,然后静置沉降6h,观察油水界面情况。结果表明,当胶体FeS颗粒超过100mg/L,静置2h时,油水发生分离,脱出污水由黑色变成淡黄色,油-水界面开始出现明显的中间过渡层;当胶体FeS颗粒含量继续增加时,油-水过渡层明显增厚。而扶余油田老化油中FeS含量高达500mg/L以上,因此可以判断胶体FeS颗粒的大量存在是老化油形成的主要原因。
3 老化油化学、氧化破乳脱水方法研究
老化油成分复杂,破乳脱水很难。大部分油田通过研制、筛选适合类型的破乳剂破坏油水界面膜以回收原油,多采用强电解质与破乳剂复配。也有油田采用特殊破乳剂使FeS转移到油相而处理老化油,但对于原油品质影响较大。本文分别采用化学破乳与氧化破乳方法来实现对老化油的脱水。
3.1 老化油化学破乳技术研究
3.1.1 化学破乳原理
破乳机理有两种:一是使乳液微粒的双电层受到压缩或表面电荷得到中和,从而使微粒由排斥状态转变为能接触碰撞的聚并状态;二是使乳化剂界面膜破裂或被另一种不会形成牢固界面膜的表面活性物质代替,使油粒得以释放和并聚。
3.1.2 化学破乳结果与分析
3.1.2.1 破乳剂类型筛选
考察阳离子与非离子型破乳剂对扶余油田老化油的处理效果,因是定性考察,药剂投加量均为2.0%,破乳沉降温度65℃,静置12h后测量老化油含水率。
乳化剂筛选实验发现非离子型OX909破乳剂对扶余油田老化油的脱水具有明显效果,且普适性能好。再进行扩展实验,确定破乳剂加量及恒温静置沉降时间。
3.1.2.2 OX909破乳剂最佳投加量
在5个100mL具塞量筒中各加入100mL脱除游离水的老化油样品(含水率63.4%),分别加入不同剂量的破乳剂OX909,振荡200次后,置入65℃恒温水浴箱中,静置24h后测定油层含水率。
由测试结果可知,对于扶余油田的老化油破乳,OX909最适合的投加量为2%,但24h内,老化油的含水率仍为16.8%,没有达到原油出厂5%的指标要求。
3.1.2.3 化学破乳最佳沉降时间
在具塞量筒中分别加入100mL处理后的扶余油田老化油,加入2%的OX909破乳剂,考察不同沉降时间下的老化油破乳脱水效果。
由考察数据可知,随着沉降时间的增加,破乳后的老化油含水率逐渐降低。当沉降时间超过48h后,含水率降低幅度不大,最佳沉降时间为48h,老化油含水率不能达到原油出厂5%的指标要求。
3.2 氧化破乳脱水研究
对于扶余油田的老化油,化学破乳难以达到既定研究目标。因此采用氧化破乳手段来解决老化油的脱水问题。
3.2.1 硝酸-硝酸钾氧化破乳机理
硝酸-硝酸盐可将已生成的硫化氢和硫化亚铁氧化成单质硫或硫酸根,破坏硫化亚铁在油水界面形成的高强度界面膜,使水滴之间易于聚结,更易于水滴与水相之间的融合。
3.2.2 氧化破乳结果分析
在5个100mL具塞量筒中各加入100mL经脱除游离水的老化油样品(1#老化油、2#老化油、3#老化油),首先分别加入不同剂量的硝酸钾,然后加入硝酸,振荡5min后,置入65℃恒温水浴箱中,静置24h后测定油层含水率。
3.2.2.1 硝酸-硝酸钾最佳投加量
由考察数据可知,对于扶余油田的老化油破乳,硝酸-硝酸钾最适合的投加量为3%,1#老化油含水率最低可达3.77%,2#老化油含水率最低可达4.97%,3#老化油含水率最低可达到3.21%,均满足原油作为商品出厂的指标5%。
3.2.2.2 最佳沉降时间
在5支具塞量筒中分别加入100mL脱除游离水的老化油(1#老化油、2#老化油、3#老化油),加入3%的硝酸-硝酸钾,考察不同沉降时间下老化油的破乳脱水效果。
由考察数据可知,随着沉降时间增加,具塞量筒顶部提取的原油样品含水率降低,沉降48h时即可获得最佳的原油回收率,而且其老化油含水率指标达到出厂要求。
4 结论
(1)扶余油田老化油含水率平均62.2%,乳化状态稳定;老化油中沥青质含量平均0.65%,胶质含量平均8.80%,老化油与净化油在沥青质与胶质含量上相差不大;老化油中固相主要是FeS胶体颗粒与机械杂质,FeS含量平均高达501.33mg/L,粒径分布为3.66~70.46μm;老化油水相中的Fe2+高达174~199mg/L;S2-高达157~209mg/L。
(2)胶质、沥青质不是扶余油田老化油生成的主要原因,胶体FeS颗粒的大量存在是老化油生成的主要原因。SRB菌代谢产生H2S,腐蚀金属材料后生成胶态FeS颗粒,胶态FeS颗粒堆积在油水界面上,形成紧密排列的刚性界面膜,促进老化油的形成。
(3)对于扶余油田的老化油破乳,OX909最适合的投加量为2%,但24h内,老化油的含水率仍为在16.8%,没有达到原油出厂5%的指标要求。采用硝酸-硝酸钾氧化破乳除硫方法处理老化油,最佳投加量为3%,沉降48h后,老化油的含水率可降至5%以下,达到出厂标准。