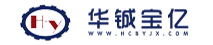
卧式螺旋卸料沉降离心机(以下简称“离心机”),具有分离效果好、全封闭运行对环境影响小、不需要冲洗且可以连续运行、系统简单、占地面积小等无可比拟的特点,主要应用于固液分离与矿的分级工艺中,广泛应用于污水处理、化工、采矿、医药等领域。在矿浆脱水、隧道盾构泥浆的处理中,因料浆中含有坚硬的石子、泥沙,且有时呈酸性或碱性,对抗磨损提出较高要求。本研究主要介绍离心机关键位置的减磨优化设计。对关键位置的优化,可降低离心机的维修率,提高其可靠性和使用寿命,从而推动行业的发展。因此,对离心机关键位置的研究,具有一定的科学价值和现实意义。
磨损对各类机械的影响较大。磨损可使间隙加大,可能增加机械的振动、冲击和疲劳,进而加剧磨损,导致机械丧失工作能力。即使不破坏,磨损也会使机械性能降低,造成工作效率降低。
磨损还是机械寿命缩短的主要因素。国外对500种典型零件的报废统计结果表明,因磨损造成的寿命缩短约占80%。磨损不仅是机械零部件的一种失效形式,也是引起其他后来失效的原因。据统计,80%的离心机失效由磨损导致,且均发生在关键位置。
1 离心机的组成与原理
离心机主要由差速器、螺旋、转鼓、机罩、机座、主电机、副电机等组成。浆料混合液经进料管进入螺旋卸料器,经螺旋卸料器进入转鼓;在转鼓高速旋转产生的离心力作用下,密度大的固相颗粒快速沉积到转鼓内壁上,与转鼓作相对运动的螺旋叶片则连续将沉积到转鼓内壁上的固料刮下并推出排渣口;分离后的上层清液经液层调节板开口从排液口流出转鼓。螺旋与转鼓之间的相对运动由差转速来实现。差速器的外壳与转鼓相连接,输出轴与螺旋相连接,输入轴与副电机相连接。主电机带动转鼓旋转的同时,也带动差速器外壳的旋转,差速器的输入轴在副电机的控制下,驱动行星轮带动差速器的输出轴旋转,输出轴通过花键带动螺旋旋转,形成一定比例扭矩的差转速传递给螺旋,实现离心机对物料的连续分离。
2 生产工况与结构参数
离心机用于选矿行业或盾构泥浆等含砂量大的工况时,磨损是主要失效形式。在铜矿浆的选铜工艺段,即选钼结束后的精尾矿处理,因为在选钼的过程中加入了铜矿物抑制剂(其作用是让铜沉下去,让钼浮上来),所以给后期的选铜带来了很多干扰。从工艺分析可知,离心机可用于选矿和洗矿工艺中,用于洗矿环节时,渣相粒径约为100目(不锈钢筛),调试参数如下:液层高度为195mm,转速为1200r/min,主机电流为75.4A,差转速为18r/min,扭矩为39N·m。进料质量分数为25.4%,进料流量为26m³/h,处理后渣含水率为23.9%,清液含固率为2.8%,详细数据如下:
进料质量分数(%) | 处理量(m³/h) | 液层(mm) | 转速(r/min) | 差转速(r/min) | 主机电流(A) | 扭矩(N·m) | 渣含固率(%) | 液含固率(%) |
25.2 | 36 | 203 | 1000 | 15.0 | 73.5 | 28 | 75.0 | 4.2 |
22.1 | 36 | 203 | 1200 | 17.6 | 78.5 | 34 | 79.1 | 4.3 |
25.4 | 36 | 195 | 1000 | 16.0 | 74.0 | 36 | 75.0 | 5.0 |
25.3 | 36 | 195 | 1200 | 18.0 | 78.0 | 39 | 75.7 | 3.6 |
25.4 | 26 | 195 | 1200 | 18.0 | 74.4 | 39 | 76.1 | 2.8 |
23.0 | 26 | 195 | 1300 | 19.5 | 76.0 | 39 | 75.5 | 2.8 |
22.0 | 26 | 195 | 1400 | 20.0 | 78.6 | 42 | 76.1 | 2.3 |
试验及试用数据均表明该机达到设计要求,但使用半年后,离心机出现了振幅增大、分离效果不稳定的情况,直接影响了正常使用。拆机检查后发现,螺旋体的卸料器磨损较严重,为保证稳定运行,迫切需要对其进行改进。螺旋卸料器非直接工作面出口附近是发生冲蚀磨损较为严重的区域,螺旋叶片也产生了不同程度的磨损,是导致失效的主要原因。
3 离心机的减磨分析与优化
固相在离心力和差转速的推动下,沿着锥度处出渣口被甩出离心机,随着二者的相对运动,势必产生磨损,合适的离心机结构对于离心机的耐磨保护至关重要。从固相在离心机内的分布可以看出,离心机易磨损的位置,一是螺旋卸料器出口处,二是螺旋锥段推料处,这两处均发生相对运动。
螺旋体是离心机的关键部件,离心机的可靠性和使用寿命主要由其决定。为了增强螺旋体的耐磨性和耐蚀性,在设计生产过程中,充分研究了材质以及材质表面的处理,包括碳化钨喷涂、镶硬质合金等方式。
开展螺旋体关键位置的技术研究,满足不同领域的需要,具有重大现实意义和社会经济效益。为离心机设计一个好“胃”,可为多个领域的发展提供良好的基础材料和技术支撑。
为了增强螺旋叶片的耐磨性,离心机设计过程中,对离心机叶片的选材进行研究(由单纯的叶片到碳化钨喷涂),选用硬质合金片,以降低整机维修率,提高设备可靠性和使用寿命。螺旋体的磨损使得脱水区压力减小,分离效果降低,必须及时更换。
针对该项目进行了合金元素调整,优化后的硬质合金片达到预期。
对螺旋体关键位置进行保护的材料选择,既保证其满足抗腐蚀要求,又有足够的材料强度满足螺旋体高速旋转的要求。此外,对螺旋卸料器的结构进行优化,实现降低磨损的目的。
3.1 螺旋卸料器的结构与减磨改进
浆料通过进料管后,由螺旋体的卸料器进入转鼓,浆料内的颗粒与卸料器出口间的相对运动伴随着磨损的产生,卸料器通常设计成“八卦形”,螺旋卸料器的出料圆弧面采用镶合金瓦或烧结碳化钨的方式进行保护,满足日常使用。而对于矿浆和含砂量较大的泥浆,实际效果不理想,出口圆弧面易产生严重磨损,影响转子的平衡,从而影响正常生产。
为了判断浆料在卸料器内的流线情况,建立了螺旋卸料器的结构模型,采用有限元软件ANSYS进行了模拟。根据以上分析,计算结果与实际运行工况完全相符,验证了数值模型的正确性及结果的可靠性。
从螺旋卸料器的出口处可以明显看出,流体在卸料器内碰撞、摩擦,其受到流向约束,进入卸料器的瞬时会有部分颗粒被甩入转鼓,部分颗粒在卸料器内回转,颗粒对内壁的反作用力体现为内壁的磨损。
由此得出,“八卦”形状的卸料器的通道与旋转作用下流体的自然流线不一致,强制流体保持流道运动,此过程伴随磨损的产生。
为避免直接磨损,采用将硬度较高的合金嵌入到卸料器内、增加出口截面积、减小停留时间等方式,对出口进行保护,并去掉了圆弧部分容易产生剪切力的区域,该种改造方式方便、快捷。
改造后的离心机在实际使用中仅延长了1个月的寿命,说明该种结构仍不理想。所以,通过提高材料硬度的方式进行保护不能够解决问题。
3.2 卸料器的结构优化
考虑到结构刚性,出料口不宜过大或过多,经过对比研究,将卸料器沿螺旋线开分配口。分配口形状采用圆形,便于对出口镶嵌合金进行保护,沿螺旋线开口也保证了对转子的刚性影响小。另外,还需要考虑浆料在卸料器内部的磨损。
为验证模拟分析的合理性,试制了样机进行验证,对各出口采用了可更换的硬质合金进行保护。实际使用情况证明该方法可大幅延长离心机的使用寿命。
4 结语
用于铜矿浆行业的卧式螺旋卸料沉降离心机分离效果较好,但需解决磨损问题。通过离散模型,对含砂量较大和矿浆领域易出现冲刷磨损的工况进行了数值模拟,找到了冲刷磨损诱因,并验证了模拟的合理性。
对易产生磨损的位置和减磨措施进行了探讨,详细介绍了适用于该行业或易磨损行业螺旋卸料器的优化设计。根据优化结果,完成了样机试制,试用结果表明达到设计要求。本研究为螺旋卸料器的优化奠定了基础,对离心机在类似行业的应用具有重要借鉴意义。