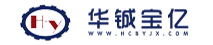
近年来,随着人们环保意识的增强和市政污水处理厂的大量兴建,离心脱水机的应用日益增多。2010年11月,环保部印发《关于加强城镇污水处理厂污泥污染防治工作的通知》,明确指出“污泥产生、运输、贮存、处理处置的全过程应当遵守国家和地方相关污染控制标准及技术规范。污水处理厂以贮存(即不处理处置)为目的将污泥运出厂界的,必须将污泥脱水至含水率50%以下”。这样一来,国内许多将污泥离心脱水后外运填埋的污水厂将受到很大影响,因为经离心脱水后污泥的含水率一般在80%左右,离国家环保部的要求有很大差距,所以这些污水厂将会考虑设备的替换。为了合理利用原有的离心脱水成套设备,有效降低设备改建成本,上海市某污水厂进行了设备改造,并通过更新升级控制系统,将原有的离心脱水系统改造成离心浓缩系统,使离心机的优势得以继续发挥。
1 整体工艺改造方案
原有污泥脱水系统的工艺流程为:污水池内的污水经搅拌机搅动后自流进入泵房,经污泥切割机打碎后,由污泥进料泵输入离心机,与配药系统配制的絮凝液在离心机内混合后,上清液通过排水管道进入中水系统进行后续处理,脱水污泥通过无轴螺旋输送器送入储泥仓,而后外运。
原来的脱水车间改为浓缩车间,而原有的储泥车间暂时保留,如果污泥深度脱水系统出现故障,可通过控制系统对离心脱水系统的运行参数进行调整,使离心机系统功能暂时恢复为脱水,并将脱水后的污泥暂时存储到储泥车间内。在改造过程中,原有脱水车间内的污泥螺杆泵(泵房内)、污泥切割机(泵房内)、配药装置、冲洗系统(泵房内)、无轴螺旋输送机等关键设备得以继续利用,同时,在车间内增设搅拌池以及浓缩污泥出泥泵(泵组)。
2 控制系统改造方案
原有离心脱水成套设备控制系统主要是用以控制污泥脱水效果(含水率保持在80%以下),而现行的改造方案要求污泥经离心浓缩后,含水率要在95%~97%(该要求为污泥下道浓缩工序提供必要的工艺准备),因此,原设备及控制逻辑需根据实际情况做出调整,而且为了满足污水处理厂关于离心机脱水、浓缩切换的要求,也需要对控制系统进行升级改造。
控制系统在两套模式中可进行切换:一为脱水模式,即将经过离心脱水后的污泥通过无轴螺旋输送机送到储泥仓中;二为浓缩模式,即将经过离心浓缩后的污泥先暂存在搅拌池中,然后再由出泥泵送出,通入储泥池。
整套系统的电气控制部分由一套系统控制柜AC1组成,用于对LW530NY污泥脱水/浓缩系统成套装置的控制。
系统控制柜AC1上电后,将开关SA1置于“屏控”后,可直接将操作权交由触摸屏进行自动、手动操作;当触摸屏出现故障后,则可以将开关SA1置于“停止”或“自动”,将操作权交还,可由控制柜面板上按钮进行控制操作。
当开关SA5置于“脱水”模式时,系统启动流程如下:
(1)液压站启动,待达到脱水频率后,指示灯长亮。
(2)离心机启动,待达到脱水效率后,指示灯长亮。
(3)无轴螺旋输送机启动,与离心机出料口连接处闸阀开启,上下连通。
(4)进料泵开启,加药泵开启,泥药混合后进入离心机脱水。
(5)脱水后的上清液自流进入厂区中水管道,污泥在无轴螺旋输送机的推料过程中进入储泥车间,由汽车外运。
当开关SA5置于“浓缩”模式时,系统启动流程如下:
(1)液压站启动,待达到浓缩频率后,指示灯长亮。
(2)离心机启动,待达到浓缩频率后,指示灯长亮。
(3)搅拌池内搅拌叶片启动。
(4)离心机出料口与搅拌池连接处闸阀开启,上下连通。
(5)进料泵开启,加药泵开启,泥药混合后进入离心机浓缩。
(6)分离后的上清液自流进入厂区中水管道,污泥在搅拌池内被搅拌均匀后,由出泥泵输送入由开关SA6指定的储泥池内,进入下一道深度处理过程中。
当系统运行周期结束,需要对设备进行保养或维护时,系统控制停机流程如下:
(1)在“脱水”模式下:进料泵停,加药泵停,切割机停→离心机降速至清洗速度→冲洗水泵启动,清洗水阀打开,进行一次清洗→清洗时间到,冲洗水泵停,清洗水阀关闭→离心机再降速至“0”→输送机关,泥饼排放阀闭→再次启动离心机,离心机升速至清洗频率→冲洗水泵启动,清洗水阀打开,进行二次清洗→清洗时间到,冲洗水泵停,清洗水阀关闭→离心机再次降速至“0”(清洗时间和次数可由人机界面设定)→液压站降速至“0”,至此设备停止完毕。
(2)在“浓缩”模式下:进料泵停,加药泵停,切割机停→离心机降速至清洗速度→冲洗水泵启动,清洗水阀打开,进行一次清洗→清洗时间到,冲洗水泵停,清洗水阀关闭→离心机再降速至“0”→浓缩后污泥排放阀关闭,污泥输送泵停,搅拌池搅拌机停,搅拌池出口阀关闭。再次启动离心机,离心机升速至清洗频率→冲洗水泵启动,清洗水阀打开,进行二次清洗→清洗时间到,冲洗水泵停,清洗水阀关闭→离心机再次降速至“0”(清洗时间和次数可由人机界面设定)→液压站降速至“0”,至此设备停止完毕。
为保证离心机系统稳定运行,控制系统会根据扭矩输出自动调整液压站频率,控制进料泵和加药泵运行和停止,对故障输出进行处理,保证脱水正常平稳运行。当扭矩大于设定P0时,液压站电机进入高速运行状态(50Hz),进料泵、加药泵进入低速运行状态(15Hz)。快速将料推出,直到扭矩小于P0时,液压站、进料泵、加药泵、切割机恢复正常运行。当扭矩大于设定P2时,输出报警,转入停机程序(不进行清洗),需要人工检修排除故障。当出现断泥、断药信号报警时,进料泵和加药泵停,当短时间恢复时,按下“复位”按钮,自动恢复进料。当离心机温度过高、振动过大、扭矩超过P2等严重事件出现时,立即停机。在“浓缩”模式下:当浓缩后污泥在缓冲罐中液位高度高于设定的高位值时,进料泵停止进料,加药泵停止加药,当液位高度低于设定的下限值时,浓缩液输送泵停止,搅拌吃搅拌机停,停止向储泥池输送。
3 浓缩模式下的运行测试
经系统改造后,在整个污泥处理流程中,设备主要用以完成浓缩工艺。为研究整套系统改造情况,在现场进行为期一个月的实地测试。以下表格为第一次调试参数记录,在该次测试过程中,需要被浓缩的污泥含水率为99.12%,絮凝剂配比浓度2‰。在进料流量40m³/h的情况下,采用液压驱动系统来驱动螺旋可使差速在运行中无级调节,当将离心机的差速由21r/min逐步下调到13r/min后,即污泥浓度由98.21%下降到96.78%,达到了含水率92%~97%的要求,此时液压站输出压力为0.9~1MPa,说明离心机受载较轻,对设备的长期运行提供了有利条件。
时间 | 离心机转速r/min | 差速r/min | 液压站输出压力MPa | 进料流量m³/h | 加药流量 m³/h | 进泥含水率% | 上清液 |
09:10 | 1620 | 21 | 8 | 40 | 0.9 | 清 | |
10:20 | 1900 | 21 | 9 | 40 | 0.9 | 98.21 | 清 |
13:45 | 1900 | 16 | 9~10 | 40 | 0.9 | 清 | |
14:25 | 1900 | 13 | 8~9 | 40 | 0.9 | 清 | |
14:50 | 1900 | 13 | 9~10 | 40 | 0.9 | 96.78 | 清 |
在浓缩后污泥含水率达到指定要求后,又进行了第二次测试,调试数据如下表所示。此次调试的目的在于,通过提高离心机的转速,设法使絮凝剂使用量降低。在该次测试过程中,进入离心机浓缩的污泥含水率为99%,配药浓度2‰。同样在进料流量40m³/h的情况下,将离心机的转速提高到2438r/min,浓缩后的污泥含水率,保持在96.83%~97.2%之间,而絮凝剂的投放量则较前次相比下降了1/3。说明在满足浓缩污泥含水率的前提下,离心机提高转速,可有效的降低絮凝剂的使用。
时间 | 离心机转速r/min | 差速r/min | 液压站输出压力MPa | 进料流量m³/h | 加药流量 m³/h | 进泥含水率% | 上清液 |
09:00 | 2100 | 10.1 | 10 | 40 | 0.6 | 清 | |
10:20 | 2100 | 10.1 | 10 | 40 | 0.6 | 97.2 | 清 |
13:00 | 2100 | 10.2 | 11 | 40 | 0.6 | 清 | |
15:30 | 2100 | 10.2 | 12 | 40 | 0.6 | 96.83 | 清 |
在浓缩后污泥含水率达到要求,絮凝剂使用量减少的前提下,还针对离心机系统浓缩性能进行第三次实验测试,数据如下表所示。该次调试的目的在于检测离心机是否能在进泥泵满负荷运转下(进泥量70m³/h)达到浓缩要求。在该次调试过程中,进入离心机浓缩的污泥含水率为99.13%,絮凝剂配比浓度2‰。随处理能力的逐步提高,加药量也相应提高。在进料流量50m³/h的情况下,假定干泥密度为1000kg/m³,药耗大约是1.6kg/h;当处理量达到70m³/h时,药耗大约是2.4kg/h。
时间 | 离心机转速r/min | 差速r/min | 液压站输出压力MPa | 进料流量m³/h | 加药流量 m³/h | 进泥含水率% | 上清液 |
09:00 | 2438 | 10.1 | 10 | 51 | 0.8 | 95.9 | 清 |
10:30 | 2438 | 10.1 | 10 | 60 | 1.1 | 93.2 | 清 |
12:45 | 2438 | 10.2 | 11 | 69.4 | 1.2 | 93.87 | 清 |
14:30 | 2438 | 10.2 | 12 | 69.4 | 1.2 | 94.23 | 清 |
与第一次实验数据对比,絮凝剂的使用量呈现上升趋势,应该是随着离心机转速的增大,絮凝作用部分失效,胶合物稳定系统被破坏引起的。可以考虑在实际运行中适当降低转速,实现药耗降低的目的。
4 结论
离心机浓缩系统性能的发挥还有一定的空间(在分离过程中絮凝剂的使用还有降低的空间)。后续可从以下几方面入手:
(1)改进混合配药系统,使絮凝剂、污泥的混合过程更充分。
(2)改进离心机腔体结构,提高离心机成套设备的污泥浓缩处理能力。
(3)根据工艺情况进一步调整成套设备控制系统,实现设备自动化操作。
现场测试,改造后的离心浓缩成套系统基本达到预期分离效果。同时,也为进行离心脱水设备改造及控制系统升级提供了原始参考,使离心机在污水处理工艺工序中的应用领域得到一定的扩展,并为后续需要转型的污水处理改造工程项目提高了有利的数据支持。