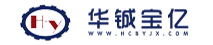
1 前言
在需要将混合物按其自然属性(液体、固体)分离的领域中,卧螺离心机被广泛地使用。特别是在大中型较发达城市的市政污水、自来水行业以及规模化固液分离领域中,卧螺离心机凭借着低劳动强度高自动化连续工作的特性,受到了广泛的青睐。
与国内外卧螺离心机相比,我国由于加工制造水平、配件互换精度和润滑辅助系统等因素的相对落后,使设备的性能在同级别型号上还存在着一定的差距,但由于国产零件以及人工成本的相对低廉,同型号类别的卧螺离心机与国外设备相比,还占据着较大的市场份额。
随着国际化进程的深入,国内人工成本的提高以及国外产品对中国巨大市场的逐步重视,采用低价方式占据市场的方式越来越相形见绌,提高产品性能,应对国内需要固液分离的复杂化混合物领域,才是实现企业盈利的有效方式。污泥与水之间存在密度差是离心分离的前提,要提高离心分离效果,增大污泥颗粒粒径和密度,减少黏度,提高离心速度是基本突破点。提高设备转速,改进润滑方式是一条较为可行的短平快路线。
2 卧螺离心机原理
卧螺离心机依靠自身高速旋转,在总成内部形成几千倍的重力加速度,使需要被分离的混合物由于自身密度不同的属性,在离心力的作用下,高密度的固相向旋转总成的转鼓壁靠拢,而密度相对较低的液体则靠近旋转中心,当混合物分离后,旋转总成内的螺旋在差速齿轮箱的作用下,与转鼓形成相对运动,将紧贴转鼓的固相物体推向转鼓锥段,在挤压下通过转鼓锥段出口排出离心机;分离后的液体随着进料的增加不断向旋转中心靠拢,分离液逆流从大端溢流口排出。
在实现分离的过程中,总成的旋转速度决定了卧螺离心机的分离因数大小,分离因数越高,混合物沉降的速度也越快;螺旋结构形式、倾斜角度、转鼓锥度决定了推料的扭矩,在旋转总成中,扭矩越大,被挤压得固体所含水分也将越低,分离效果也就相对较好。
转速的提高,可使密度较接近的混合物在有限的空间(卧螺离心机的总成容量)及时间(混合物由进入设备到排出设备的间隔)内,快速分离并达到分离要求。
在机械结构允许的范围内提高设备转速,可能对轴承的性能、寿命以及润滑介质提出较高的要求。因为考虑到设计制造成本,设备安装便捷性,维护便利性、市场满足度等因素,常规的卧螺离心机主轴承采用的润滑方式多为油脂润滑。
为满足高分离因数市场的需求,在不对原有设备尺寸进行大规模调整的情况下,将轴承座的润滑方式改变为稀油润滑将可能是一个有效的方案。
3 卧螺离心机轴承座结构改进
3.1 油脂润滑轴承座与稀油润滑轴承座
常规油脂润滑的轴承座优点主要有:
(1)拆装简便。对装配人员的工作技能要求不高。
(2)加工精度要求不高。上下轴承座的结合面表面粗糙度要求较低,整个轴承座除轴承接触面,安装面以及固定螺栓尺寸等要求外,其余加工尺寸均较宽松,且密封采用填料方式,可弥补加工尺寸的不足。
(3)制造成本较低。加工精度要求较少,加工复杂程度则较低,使整个加工工时较少,人工成本下降。当卧螺离心机转速提高,旋转总成的dn值增加,常规使用的脂则无法达到润滑与降温的要求。高转速脂的价格较常规使用脂价格而言成几何级数增长,由于脂的损耗性,更换脂型号将导致配件成本的直线上升。
以上海市离心机械研究所有限公司LW530设备为例,长期以来,应用于众多行业领域的使用转速为2200r/min左右,主轴承d为180mm,dn值为396000;而为应对市场需求,此次制造的LW530工作转速要求达到3100r/min,dn值达到了594000。按机械手册建议dn值超出400000,采用稀油润滑更为合理。因此,在不改变LW530整体结构的基础上,对主轴承的轴承座进行结构再设计,将是满足设备旋转速度的关键。
按机械手册关于稀油润滑轴承座标准进行设计,两主轴承座的宽度均需要再放大20mm,尤其是靠旋转总成的两个面,如此设计将增加旋转总成的长度,影响旋转总成的刚度,整个设备的处理容积,旋转振动频率,结构壁厚均要重新计算;同时需要将设备底架进行放大,这无疑是重新设计一台离心机,对于时间短,成本控制要求严格的该项目而言是不可行的。
综上所述,在保证设备整体尺寸不变动的情况下,在原有轴承座空间位置内对轴承座及润滑方式进行再调整才是保证设备满足用户需求的唯一可行方案。
3.2 双油路设计与自除渣方法
稀油润滑轴承座需要解决如下问题:首先是空间限制,需要确立一套合理的内部结构及密封方式来确保不出现漏油问题;其次是润滑充分,除需要考虑设备在正常运转过程中的润滑外,还需要确保在突发状况下设备的润滑要求。
常规稀油润滑轴承座通常对喷射口的位置、轴承座尺寸、被润滑的轴承型号有着限制。在规定轴承型号的前提下,普通喷射口的位置基本采用的是对准轴承滚子喷射,由于是90°直喷,油液反弹,飞溅明显,如果没有足够空间及精确的密封配合尺寸,容易产生轴承座漏油的现象;采用型号轴承,喷淋口由轴承上方口流入轴承滚道,降低了反溅,但受该型号轴承转速限制,无法满足卧螺离心机的设计要求。
采用双油路设计,常规润滑依靠滚子自身旋转以及油液自流的方式达到与滚子接触的目的,利用金属软管的可弯曲性以及位置形状保持性,将两根喷淋用油管分别架设到主轴承靠近轴承座上方的左右两侧,同时对轴承滚子进行喷油,提高了油与滚子的接触面积,使润滑有效性提升的同时,也达到了加快带走轴承热量的目的;从轴承的两端沿轴承的旋转方向对轴承滚子进行喷淋,由于与滚子接触角度减小,接触点由于是与轴承旋转方向一致,反射得到了有效控制,接触性相比垂直于轴承旋转方向的接触也更加的合理。
由于润滑采用的是系统供油,由于轴承座原有结构的限制,轴承安装与轴承座的轴承档较高,无法实现在现有结构中保证有部分油始终能浸没轴承滚子,一旦系统故障失电,喷油停止,而轴承座内部的润滑油由于重力作用回流进油箱,高速旋转的卧螺离心机停机时间在3min以上,没有润滑的轴承在高速旋转中由于发热将直接导致烧毁。
为此,在轴承档除增加半月环储油,喷淋后的油将流入储油环中,实现轴承底部的滚子始终浸没在油中,保证了润滑,一旦发生短油问题,则可确保设备在停机旋转过程中不烧毁轴承。
由于半月环中的油始终会有部分残留,长时间的选择使油液中不可避免地含有杂质,如果杂质长期残留在油中,将对轴承造成严重后果;定期拆卸轴承座,依靠人工方式除去半月环中的杂质,不但容易引起因经常拆装轴承座损坏结合面的问题,而且会因为清理影响设备长期连续运行,降低生产效率。
采用一种除渣结构,通过电气设定自动控制,可帮助处理杂质残留问题。除渣结构的工作原理是,在半月环下开设放空孔,通过一根由轴承座外部斜拆而入的连杆将孔封住,通过轴承座外部弹簧的拉力使连杆始终处于关闭放空口的状态,通过设定时间,触动电信号,当需要放空油液时,提拉连杆即可达到排除杂质的目的。
3.3 密封结构设计
为防止飞溅油液的泄漏,考虑上下轴承座安装的便利性,轴承座采用径向密封的方式。由于设备高速旋转,常规径向密封无法完全阻止油沿着密封间的间隙渗漏出轴承座,因此将轴承座内部结构进行调整。
(1)增加静态插片型档液板,依靠螺栓与轴承座上盖连接,使被反弹的油液在未达到轴承座壁前就较大限度地降低飞溅速度。
(2)部分未被挡液板拦截的油液仍会飞溅到轴承壁上,但数量大幅减少,此时的液体仍可沿密封间隙向外流出,但动能基本消失,在密封结构的外侧去除旋转环密封片,防止油液接触旋转环密封片飞出,采用空腔收集油液,在空腔下部开设斜孔引导油液回流入轴承座内。
(3)在重力作用下的油液会沿静态插片落在旋转轴上,部分油液会沿旋转轴向轴承座两侧爬行,为尽可能多地阻挡油液向密封环靠拢,在旋转轴上开设螺旋线,在旋转轴运动过程中,两端螺旋线的旋转方向均指向轴承。
(4)在轴承座顶端开设直径23mm通气孔,排出轴承座内部空气,减低轴承座内部压力。
通过上述方面的结构调整,在测试平台上模拟运行,转速为3300r/min,进油流量为1.5L/min,测试时间为3h,轴承座底端的油液收集槽内未发现有明显油液渗漏。
3.4 电气温度控制设计
为使润滑系统满足设备运行要求,针对轴承座内轴承温度的实时监测,采用一种卧螺离心机的温度控制方法来达到确保设备在高转速下稳定运行。
控制方法原理:控制器输出初设给定值至润滑系统变频器,使变频器工作于初始工作频率25Hz后起动润滑机构的电动机,在泵送作用在润滑油量达到工作流量0.5L/min;随后起动卧螺离心机,进料机构及加药机构开始进料(混合物);温度继电器将设于稀油润滑轴承座上的温度传感器实时反馈的温度信号传送至控制器中;控制器将实时反馈的温度信号与控制器中预设的温度值(T0、T1、T2和T3)进行比较后,发出相应的控制信号至进料、加药量以及水冷机构对轴承进行降温。
其中T0预设温度值为60℃,T1预设温度值为70℃,T2预设温度值为80℃,T3预设温度值为90℃,控制器接收到的实时反馈温度信号为轴承温度T。当T≤T0时,控制器控制变频器的转速保持在25Hz,使得润滑机构的润滑油流量保持在0.5L/min;当T0<T≤T1时,控制器控制变频器的频率随温度的升高按线性比例增加,调整范围在25~50Hz,增加进油量,加快油液流动带走轴承热量;当T1<T≤T2时,控制器控制变频器的频率保持在50Hz,同时控制器发出控制信号开起卧螺离心机中的水冷机构;当T2<T≤T3时,控制器控制变频器的频率保持在50Hz;保持水冷机构处于开启状态;控制器发出控制信号关闭进料机构及加药机构,卧螺离心机停止混合物处理;当T3<T时,控制器控制卧螺离心机停机并发出报警信号。
采用本发明的温度控制方法可以时时把安装在轴承座上温度传感器测试的温度转化成信号及时反馈给控制器,根据温度的变化,控制器能够及时地调整卧螺离心机的降温方案,避免轴承因高温而损坏。
4 设备实际应用
在经过6个月的针对LW530卧螺离心机的再设计及制造后,将16台套设备准时交付给了某城市多台套联动印染污泥水处理项目,经过3个月的设备安装以及调试,实现分离印染污泥混合液过程中,达到进料浓度3%~5%,设备转速3100r/min,单机处理量45m³/h,出泥含固率20%,出液SS值小于700的效果。设备主轴承温度及润滑系统工作参数如下:
序号 | 转速 | 差速 r/min | 进料浓度 % | 进料流量 m³/h | 加药浓度 % | 加药流量m³/h | 加药量 kg/t | 出渣含固率 % | 分离液SS 10-4% | 左轴承温度 ℃ | 右轴承温度 ℃ |
1 | 2750 | 12.1 | 3.1 | 45.2 | 2 | 4.2 | 8.97 | 19.43 | 800 | 45 | 43 |
2 | 2750 | 9.2 | 3.1 | 38.9 | 2 | 4.2 | 9.06 | 20.15 | 750 | 47 | 43 |
3 | 3010 | 12.3 | 3.1 | 45.2 | 2 | 4.2 | 9.09 | 22.1 | 730 | 52 | 50 |
4 | 3010 | 9.1 | 3.1 | 39.8 | 2 | 4.2 | 9.09 | 19.01 | 730 | 50 | 48 |
5 | 3010 | 8.7 | 3.1 | 46.8 | 2 | 4.3 | 9.13 | 19.76 | 700 | 52 | 48 |
6 | 3100 | 12.1 | 3.1 | 51.2 | 2 | 3.5 | 7.63 | 16.21 | 600 | 50 | 50 |
7 | 3100 | 12.2 | 3.1 | 50.5 | 2 | 4.3 | 9.13 | 18.08 | 650 | 52 | 48 |
8 | 3100 | 9.3 | 3.1 | 52.1 | 2 | 4.4 | 9.49 | 19.37 | 630 | 52 | 48 |
由上表中看出,连续运行的卧螺离心机主轴承的温度始终保持在50℃左右,经过振动仪器以及离心机四面两侧的噪声测试,均保持在86dB以下,且无异常现象,说明轴承座的使用达到了预期的效果。
5 结论
(1)采用稀油润滑轴承座,在不改变原有LW530卧螺离心机整体结构和尺寸下,达到了设备设计要求的工作转速3100r/min。
(2)通过增加静态档液板,预留轴承座外档密封环,旋转轴开设推油螺旋线,增设密封环回油斜孔的方式,解决了因空间局限而可能出现油液泄漏的问题,使设备运转环境保持清洁。
(3)采用轴承两侧依靠金属软管沿轴承旋转方向供油润滑的形式增加接触面积,加快散热的同时,考虑极端条件下断油轴承保护,增加浸润结构的同时,还加装除渣装置以及轴承温度控制方式,有效降低了轴承过热烧毁的可能性。双油路自除渣润滑轴承座的使用,使设备转速得到了明显提升,为设备深化应用领域提供了必要的技术保障。