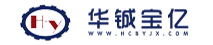
卧螺离心机是一种通过转鼓与螺旋输送器进行同轴差速转动、使物料完成固液分离的离心分离设备。由于具有可连续运行、处理量大、适用范围广、节能和生产现场环境好等优势,卧螺离心机在很多行业中得到应用。卧螺离心机结构参数是影响卧螺离心机分离性能的重要因素之一。在操作参数与物性参数不变的情况下,如何通过改变卧螺离心机结构参数来提高出渣含固率与固相回收率一直是国内外学者的研究重点。
现有关于卧螺离心机结构参数的研究主要是通过调节转鼓或螺旋输送器结构参数改进卧螺离心机分离性能。代朝辉研究了转鼓结构对卧螺离心机分离效率的影响;荆宝德等探究了转鼓锥角结构对用于处理建筑水泥的大直径卧螺离心机分离性能的影响,提出了一种双锥角结构;邱发华等讨论了进口入射角对内部流场的影响并选取了较佳进口入射角度;PEETERS等研究了液池深度对卧螺离心机分离性能的影响。
卧螺离心机的螺旋起到输送沉渣与挤压脱水的作用,螺旋结构参数关系到卧螺离心机分离性能的好坏,是卧螺离心机核心部件。目前关于卧螺离心机螺旋结构的研究主要以改善清液回流为目的,提出了一些新型螺旋结构。一些国内学者与工程技术人员为使清液快速流出,依据传统的活塞式流动理论提出了镂空式螺旋;为缩短清液回流路程,孙启才等提出间断式螺旋结构。本文针对文献中提到的新型螺旋结构进行流场数值模拟研究。
1 计算模型与网格划分
根据某厂家提供的LW-250型卧螺离心机结构数据为基础,在不影响模拟结果的前提下对转鼓小端的排渣机构做出适当简化后建立模型。采用Solidworks软件建立LW-250型卧螺离心机结构三维模型。建模结果如下:
名称 | 参数 | 数值 |
转鼓几何尺寸 | 转鼓内径(mm) | 250 |
半锥角(°) | 8 | |
柱段长度(mm) | 625 | |
锥段长度(mm) | 375 | |
螺旋几何尺寸 | 螺旋内筒半径(mm) | 170 |
叶片倾角(°) | 0 | |
螺旋螺距(mm) | 60 | |
叶片顶隙(mm) | 2 |
镂空式螺旋结构提出的依据是传统的活塞式流动理论(∑理论),该理论认为液体在转鼓内的流动是活塞状的。按照这个假设采用镂空式的螺旋结构可使分离出的清液迅速流出,增加卧螺离心机的处理能力。
间断式螺旋的设计目的是为了使分离后得到的清液沿较短流程流出,转鼓沉降区的螺旋叶片采用了若干对错式结构,每段结构的轴向长度Sd由该段螺旋的旋转角度φd确定。本研究中分别将φd取值为1.5π,2π,2.5π和3π,即螺旋叶片每旋转对应角度就设置一处断开式结构,断开间距取5mm。
研究使用Solidworks建立模型并导入ICEM中进行网格划分。考虑到螺旋输送器部分模型复杂的原因,网格采取分区建立的方法生成,转鼓结构建立结构化网格,螺旋输送器部分建立非结构化网格。
2 湍流模型与边界条件
2.1 湍流模型与多相流模型
董连东等分析了现有湍流模型在卧螺离心机流场模拟中的准确性,发现在较高转速下雷诺应力模型的数值模拟结果较接近实际情况。由于卧螺离心机内部流场流动复杂且存在高速旋流,因此在研究中使用雷诺应力模型。
在卧螺离心机脱水的实际应用中,转鼓内物料的浓度变化范围较大且变化速度较快,因此采用多相流模型进行数值模拟。由于Mixture模型中包含体积分数方程与滑移速度方程,能够对卧螺离心机转鼓内物料分离过程进行更好地描述,因此在研究中采用Mixture模型。
2.2 边界条件与求解方法
模拟中进料管入口采用速度入口边界,由处理量计算入口速度V0=1.2m/s,垂直于进料口进料,出口采用Outflow边界,所有壁面都采用无滑移边界和默认粗糙度。
模拟中固相颗粒设置为滑石粉。由Malvern激光粒度仪对实验室现有滑石粉物料进行粒度测试,测得颗粒中径为28.7μm,体积平均粒径为32.6μm,取其平均值30μm作为模拟颗粒粒径,入口固相体积分数设为30%。研究结果表明,尽管颗粒粒径不同,但转鼓内沉渣含湿量沿轴向呈现相同的变化规律,固相回收率也随着颗粒粒径的增大而增大。因此采取单一粒径进行数值模拟的结果仍然可以为其他粒径分离结果提供参考。模拟采用多重参考系模拟同轴差速转动,转鼓转速为2520r/min,与螺旋输送器之间的差转速为20r/min。
文章中的求解方法采用分离、隐式算法。采用SIMPLE算法耦合压力与速度模型,压力离散格式采用PRESTO,其余则采用精度较高的QUICK格式。
3 计算结果与分析
为评价卧螺离心机的分离性能,引入出渣含固率W、固相回收率E与含湿率F作为评价指标。根据螺旋输送器设计理论,螺旋叶片的主要作用是对沉渣进行进一步的挤压脱水与输送沉渣,同时螺旋叶片也为转鼓内液体与颗粒的流动提供稳定的旋流边界。螺旋叶片的形式对转鼓内沉渣的分离与输送都有着重要的影响,此时几种螺旋对分离的影响可分析如下。
3.1 常规螺旋卧螺离心机的流场
常规螺旋卧螺离心机由于螺旋叶片的存在,沉降至转鼓壁面的沉渣都被螺旋叶片输送至转鼓锥段进行进一步的挤压脱水,因此沉渣在转鼓内的堆积高度与浓度都随着锥段直径的缩小而增大。在转鼓沉降区,沉渣在单个螺旋导程内都呈现弧形凸起状的分布。同时,转鼓内分离完成的清液会沿沉渣内侧的螺旋通道回流至转鼓大端,而后从溢流口排出。转鼓内固相与液相的变化规律与波尔茨利用偏振光法测定各项变化规律相同。
在转鼓沉降区脱水速度极快,沉渣内的大部分水分在很短的轴向距离内就被脱去。沉渣进入过渡区时含湿量已经处在较低的水平,脱水速度比较缓慢。此时含湿量的迅速稳定可以代表沉渣的脱水过程在过渡区就已经基本完成。转鼓内沉渣含湿量的变化规律与波尔茨用放射性同位素标记的测量结果以及工业应用中的实际情况基本一致。
3.2 镂空式螺旋卧螺离心机的流场
对镂空式螺旋来说,由于柱段螺旋镂空的原因,转鼓柱段已经不存在传统的螺旋型流道结构。镂空式螺旋流场内的轴向速度在转鼓横、纵截面均有规律可循,镂空区域交替分布着不连续的、轴向速度相反的两种旋流。此时,转鼓柱段的旋流可分为3层,外侧沉渣所在区域的旋流、中部剩余螺旋所维持的旋流以及内侧镂空区产生的交错旋流。
然而由于活塞式流动理论过于粗糙,与实际的流动情况差别很大,特别是对于柱-锥型转鼓结构,离心机内的流动应存在多个速度分量,清液的排出并不是完全轴向的。在目前更被认可的层流流动理论的假设条件下,镂空螺旋产生的实际作用应有不同。由于转鼓柱段沉降区的流场已经遭到破坏,颗粒虽能沉降但无法顺利输运,只能堆积在转鼓两端,转鼓中心则堆积大量清液,叶片去除高度越高,清液堆积越多,此时,虽然转鼓锥段的螺旋仍起作用,但影响相当有限,分离效果并不理想。不仅如此,镂空式结构还会导致叶片刚性下降,因此在实际中使用不多。
3.3 间断式螺旋卧螺离心机的流场
采用间断式螺旋时,转鼓内的轴向速度分布比较合理,但在间断处也会产生局部扰动。由于扰动具有局限性,可以发现改变间隔距离不会对转鼓内的固相分布产生很大影响。转鼓锥段采用了传统螺旋,因此轴向速度变化不大。
采用几种不同螺旋结构可以发现,采用镂空式螺旋的卧螺离心机分离性能较差,固相回收率与出渣含固率均低于常规螺旋;间断式螺旋与常规螺旋分离效果相差不大,同时考虑到间断式螺旋制造麻烦,且强度较低,因此在设计中应当慎重采用。
4 结论
采用Mixture多相流模型、雷诺应力湍流模型对卧螺离心机应用中的常规螺旋、镂空式螺旋和间断式螺旋进行三维数值模拟,分析了不同螺旋叶片结构对卧螺离心机内部流场分布特性与分离性能的影响,得出如下结论:
(1)使用常规螺旋时,卧螺离心机内沉渣在螺旋输送器的作用下输送至转鼓小端由排渣口排出,清液回流至转鼓大端由溢流口排出,沉渣在转鼓内的堆积高度与浓度都随着锥段直径的缩小而增大,沉渣在沉降区脱水速度极快,进入过渡区后脱水速度下降至稳定状态,脱水过程基本完成。
(2)使用镂空式螺旋时,镂空区域形成了交替分布且轴向速度相反的流动状态,固相向转鼓两段堆积而清液向转鼓中段流动,由于活塞流动理论这一假设并不符合实际流动状态,镂空螺旋并没有达到提升分离性能的目的,分离性能下降。
(3)使用间断式螺旋时,转鼓内轴向速度分布比较合理,仅在螺旋间断处产生局部扰动,改变间隔距离对转鼓固相体积分数分布影响较小,与常规螺旋的分离性能相差不大,但制造麻烦,强度较低,不建议选用。