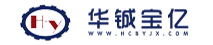
卧式螺旋沉降离心机应用范围广,能广泛应用于多个行业污泥脱水的场合;对物料的适应范围较大,可以分离固相粒径为0.005~2mm,固相浓度为0.5~40%的悬浮液;能自动、连续运转,装机生产能力大,运行维护费用较低,因此,卧式螺旋沉降离心机在含油污泥脱水系统中得到广泛应用。
在生产过程中,卧式螺旋沉降离心机出现开机差速报警或振动报警、主机报警停机、脱水后的污泥含水率不稳定、离心机不出泥、螺旋推进器外圈磨损严重的问题。本文根据大庆油田生产运行的实际情况,结合卧式螺旋沉降离心机的工作原理、结构组成,分析了卧式螺旋沉降离心机在含油污泥脱水系统中故障产生的原因,提出解决故障的有效措施,总结了使卧式螺旋沉降离心机稳定运行的管理方法。
1 工作原理
卧式螺旋离心机是一种螺旋卸料沉降离心机。主要由高转速的转鼓、与转鼓转向相同且转速比转鼓略低的带空心转轴的螺旋输送器喝差速器等部件组成。当要分离的悬浮液由空心转轴送入转筒后,在高速旋转产生的离心力作用下,立即被甩入转鼓腔内。高速旋转的转鼓产生强大的离心力把比液相密度大的固相颗粒甩贴在转鼓内壁上,形成固体层(因为环状,称为固环层);水分由于密度较小,离心力小,因此只能在固环层内侧形成液体层,称为液环层。由于螺旋喝转鼓的转速不同,二者存在有相对运动(即转速差),利用螺旋和转鼓的相对运动把固环层的污泥缓慢地推动到转鼓的锥端,并经过干燥区后,由转鼓圆周分布的出口连续排出;液环层的液体则靠重力由堰口连续\溢流\排至转鼓外,形成分离液。
2 常见故障分析及对策
2.1 开机差速报警或振动报警
卧式螺旋沉降离心机开机差速报警停机或启动时声音异常,振动比较大,造成报警停机。造成这两种报警停机的原因是停机时冲洗不彻底或冲洗程序不正确,冲洗不彻底一是导致离心机排泥端泥渣积存过多,再次起动时造成转鼓和螺旋之间差速过高报警;二是转鼓的内壁上残留不规则固体残渣,当离心机启动时造成转鼓运动不平衡而产生振动报警。出现上述两种停车报警后,按复位键,当转速升高到300r/min以上时松开,待转速达到500r/min以上时开始打开冲洗阀冲洗,当低速冲洗不彻底时,打开机盖将自来水管伸进转鼓进行人工清洗,直至彻底冲洗干净。正常停机冲洗时,判断是否达到预期效果主要看扭矩值,扭矩值小于1KNm表示冲洗比较干净;非正常冲洗时,判断是否达到预期效果使齿轮轴保持不动,用手转动转鼓,转鼓转动是否灵活,如果转动不灵活,用水彻底清洗干净。该工作需在停机时马上进行,因为在未启动机器中清除沉淀物是比较容易的。
2.2 脱水后的污泥含水率不稳定
离心机正常的出泥含水率在75%,但运行了3个月发现出泥的含水率时高时低,高时达到90%,低时达到70%,分离液浑浊,含固率在1%左右,高达3.8%,运行非常不稳定。出现离心机出泥含水率不稳定的主要原因是离心机的进料量不均匀,污泥经化学热清洗罐处理后,上层为浮渣和油回收利用,中层为悬浮液,底层为油泥,底层的油泥直接用污泥泵送至离心机脱水,由于化学热清洗罐进料不是连续的,造成罐底层的污泥厚度时高时低,污泥泵的运行时间不易控制,造成进入离心机的污泥含水率不稳定。
针对上述问题,及时调整了工艺流程,增加了污泥罐,将化学热清洗罐的底层污泥排到污泥罐中,污泥罐中加入搅拌机,搅拌均匀后再用污泥泵送至离心机,经过一个月的运行,离心机脱水基本稳定。
2.3 螺旋磨损严重
离心机开机启动时,声音和振动出现了异常,进料后异常声音消失,打开机罩检修,手动盘车,转鼓和螺旋正常,检查发现螺旋片磨损严重,尤其是锥体部分磨损严重。
螺旋片磨损的主要原因是污泥中含有泥砂较多,污泥是多种性质不同的混合物,如钻井污泥、压裂返排液污泥、酸化污泥、清淤污泥等,有的污泥含泥砂较多,有的还有腐蚀性,造成螺旋的磨损。
针对上述问题,及时调整了工艺流程,在离心机前采用重力沉降或旋流除砂器,将大颗粒的砂粒除去,降低污泥中含砂量,经过一个月的运行,离心机运行稳定,检修发现离心机磨损问题得到了改善。
3 稳定运行的管理方法
(1)减少离心机的振动。每次停机后对转鼓和螺旋进行彻底清洗。
(2)降低离心机螺旋的磨损。采用重力沉降或旋流方式减少污泥的含砂量。
(3)定期清洗污泥返流管,返流管堵塞,污泥含固率下降,离心机产生振动。
(4)定期清洗离心机给料污泥泵,防止污泥泵堵塞造成离心机被迫停机。
(5)絮凝剂投加装置的维护。定期清理絮凝剂投加装置上的管道、搅拌器、静态混合器上的粘团和结块,防止堵塞。
(6)严格按着操作说明书进行日常维护和保养。
4 结论
本文研究了卧式沉降离心机的结构原理,结合现场的实际运行情况,分析了离心机产生开机差速报警或振动报警、脱水后的污泥含水率不稳定、螺旋磨损严重的原因,找到了相应的解决方法,并总结了离心机稳定运行的管理办法,经过三个月的现场运行跟踪,设备运行基本稳定。