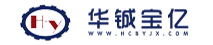
沉降式离心机是藉固液密度不同,在离心力场作用下实现固液分离的。其作用是从动力堆乏燃料溶解液中去除不溶物固体。我国沉降式离心机的研究开始于1987年,其发展过程大致经历了从科研样机的开发、吉化厂制造的沉降式离心机的水负载试验失败、西塘化工机械有限公司承制的沉降式离心机模拟料液试验成功三个阶段。整个研发过程一波三折,凝聚了多位专家的心血,实现了由科研机向工程机的过渡,它填补了国内空白,为我国核燃料后处理固液分离工艺开创了一个新局面。它核其他料液过滤器相比:过滤速度快,生产能力大,还可避免更换滤芯子所产生的大量固体废物,能适应大生产能力核燃料后处理厂的需要。
1 沉降式离心机主要结构特点
1.1 轴系
沉降式离心机有刚性轴和挠性轴之分。一般对运转速度不太高,转子直径较大,液体流动性较好的离心机通常设计成刚性轴。原科研机设计为刚性轴,它的转鼓轴轴颈较大(Φ125mm),其临界转速大于工作转速,转鼓轴与支撑轴承的间距大(800mm),设置了大尺寸的轴承,整个转动轴系的高度也相应减小,由于没有过临界转速时的振动问题,其减振结构相应简化,取消了挠性轴常需的球形支撑。其优点是工作转速低于其一阶临界速度,没有过临界转速时的振动问题,可以在较宽的速度范围内操作。刚性轴本身结构可设置大尺寸的轴承,此轴承的受力状态较好,可提高整机的寿命。其缺点是拆装和检修不易实现全远距离操作。
考虑到离心机转鼓全远距离检修的要求,工程机采用了与科研机完全不同的传动轴系结构。工程机转鼓轴轴径较小(Φ80mm),转鼓轴与支撑轴承的间距较小(约300mm),整个轴系高度增大,增加了挠性轴常需的球形支撑。其优点是可通过检修容器SSERC,吊装转运及更换转鼓,实现远距离维修。但挠性轴也带来了其他缺点:增加了挠性轴常需的球形支撑和相配套的减振结构(减振弹簧-阻尼器);其工作转速高于一阶临界转速,过临界转速时的振动较大;且工作转速范围宽,沉降分离时转速约2500r/min,排渣转速约20r/min,在这样宽的速度范围内工作,转动过程中影响转动平稳的因素较多。工程机与科研机轴系结构及优缺点如下所示:
项目 | 科研机 | 工程机 |
轴系类型 | 刚性轴 | 挠性轴 |
轴径尺寸(mm) | Φ125 | Φ80 |
轴承间距(mm) | 800 | 约300 |
球形支撑 | 无 | 有 |
减震系统 | 简单 | 减震弹簧-阻尼器 |
一阶临界转速 | 高于工作转速 | 低于工作转速 |
优点 | 没有过临界转速时的振动问题,轴承的受力状态较好,可提高整机的寿命 | 在强放射性区域内没有轴承等易损件,拆装和检修可实现远距离操作 |
缺点 | 在强放射性区域内有轴承等易损件,拆装和检修不易实现远距离操作 | 工作转速高于一阶临界转速,过临界转速时的振动较大,转动过程中影响转动平稳的因素较多 |
1.2 转鼓结构与进料方式
从近年来国外发展的离心机研究资料来看,转鼓结构有正杯型和倒杯式,对应的进料方式有上进料和下进料方式。国外沉降式离心机主要特点如下:
厂家、型号 | 结构特点 | 转鼓 | 料液特点 | 运转参数 | 清液质量 | 备注 |
1976法国UP2厂 | 上进料,高压水冲洗排渣,挠性轴有防护及临界安全性能,可用屏蔽检修装置更换易损部件 | 正杯型 Φ500 L420 | 压水堆元件溶解液 | 2100r/min 1209g Q=225L/h | 理论截留0.2μm | 有DPC210,500,800,900,投入运行,存在排渣不畅的缺点 |
1981英国 | 同上 | 正杯型 Φ800 L520 | 压水堆元件溶解液 | 2000r/min 1800g | 0.5~1.5μm η=0.94~0.99 | |
1959英国唐瑞快堆 | 空气透平驱动,自吸上料,转筒和沉渣一起拆下做固体废物 | Φ50 L250 | 快堆元件溶解液 | 20000r/min 11000g Q=180L/h | η=0.999 | |
1980美国快堆模拟ShovplesP-850 | 立式,螺旋连续排渣 | Φ150 | 固粒比重1.2~2.45 液体比重1~1.43 | 12.2~2.47L/min 529~1080g | η=0.96~0.994 0.5μ | |
1988意大利1TRECCSTT-1 | 下进料,高压水冲洗排渣,热室内安装,可遥控更换易损部件 | 倒杯式 Φ800 | 颗粒1μ 0.3μ, 0.03μ MoO2 Al2O3 | 4500r/min 9000g Q=100L/h | η=0.99 | |
西德 WA=350厂 | 上进料,高压水冲洗排渣,电机与转筒共轴,有弹性减震装置可以用机械手遥控更换损坏部件 | 倒杯式 | 压水堆元件溶解液 | 2000g | 1983年在WAK的Teko进行冷料试验,WA-350厂已停建 |
我国的科研机和工程机都采用倒杯式转鼓和下进料方式,其优点是缩短了主轴长度,简化上部结构,并使排渣畅快,操作时对上方污染少。工艺管道集中布置在转鼓的下方,有利于转鼓的起吊、检修和解决α密封。
下进料是通过空气提升方式,料液自下而上从进料管喷嘴喷到转鼓上部,并借助于与转鼓同步高速旋转的散液板将液体甩到转鼓的壁上完成进料操作。
1.3 出料及排渣方式
工程机设置有清液室、锥筒及渣口切换装置。清液室由锥形底与筒体连接形成的环形槽,内有清液出口管。高速水流呈螺旋状飞溅到外壳上进入清液室。
锥形底位于筒体下部,锥筒上固定有上料管喷嘴、高压水喷嘴及排渣口(回流口),渣口切换装置位于锥形底下部,它由核级阀门电动装置、穿地轴、锥筒等组成。切换罐底部设有回流管口(回流入料液槽)、排渣管口(进入渣水槽)和挡板,当在高速沉降分离时,锥筒对准回流口使得上料过程中由于上料管与散液盘之间空隙的存在,料液沿上料管外壁的回流液以及液体和气体摩擦,进料和散液板之间的碰撞形成雾滴通过锥筒收集经回流口进入料液槽。据了解,由于科研机没有此装置,在分离操作时,从渣口收集的原液量是进料量的1‰,就与形成的雾滴有关。排渣时,锥筒对准排渣口,4个90°扇形喷嘴的水流将覆盖转鼓内壁,在慢速转动情况下实现冲渣,渣水通过锥筒进入渣水槽。
2 水力学特性
2.1 流体自由液面的形状
流体在重力场和离心力场的作用下,自由液面呈抛物面形,转鼓的尺寸和转速决定液面形状,在转鼓溢流口(Φ395)以下,液体飞落入清液室,由下式可以计算液面形状:
X2-X20=2(900/n2)Y
式中:
X:液面上某一点与旋转轴的距离,m;
X0:溢流口半径,m;
Y:液面上某一点至溢流口面的距离,m;
n:转速,r/min。
离心机的分离因数Fr是离心加速度和重力加速度的比值,离心机的分离因数按转鼓内径计算(Φ500)。由下式可以计算分离因数Fr。
Fr=Rn2/900
式中:
R:转筒半径,m;
n:转速,r/min。
转鼓高速转动时,形成的流体自由液面的形状用转鼓内不同高度处的液层厚度b表示。则不同转速下的自由液面的形状及分离因数见下表:
n(r/min) | 2500 | 2000 | 1500 | 1000 | 800 | 500 | 300 | 200 | 100 | 50 |
Fr | 1736 | 1111 | 625 | 277 | 177 | 69 | 25 | 11 | 2.7 | 0.69 |
V/L | 34.3 | 34.3 | 34.3 | 33.1 | 31.3 | 28.9 | 26.5 | 18.8 | 4.0 | 0 |
Y(mm) | b(mm) | |||||||||
400 | 52.2 | 52.2 | 51.7 | 50.7 | 50 | 45.5 | 31 | 12 | 0 | 0 |
300 | 52.3 | 52.3 | 51.9 | 51.3 | 50.6 | 47.3 | 36 | 21 | 0 | 0 |
200 | 52.4 | 52.4 | 52.1 | 51.6 | 51.3 | 50 | 40.3 | 31 | 0 | 0 |
100 | 52.5 | 52.5 | 52.3 | 52.1 | 52 | 50.9 | 46 | 42 | 11.5 | 0 |
50 | 52.5 | 52.5 | 52.4 | 52.3 | 52.3 | 51.8 | 50 | 47 | 31.2 | 0 |
30 | 52.5 | 52.5 | 52.5 | 52.5 | 52.5 | 52.5 | 52.5 | 52.5 | 52.5 | 0.04 |
2.2 流体流动状态
转鼓高速转动时,厚液在重力和离心机作用下向下流动,清液从转鼓溢流口进入清液室,可以按照活塞理论和层流理论分析流体流动状态。
活塞理论者认为,流体在转鼓内横断面上均匀等速向下流动,可根据转鼓内流体存留量和进料速度计算出液体在转鼓内的停留时间。
下表是按活塞理论计算与实际试验时停留时间的对比。可以看出,试验值与计算值比较一致,符合活塞理论。
进料量 | 平均停留时间(r/min) | |
计算值 | 试验值 | |
200 | 10.29 | 11 |
350 | 5.88 | 7 |
500 | 4.12 | 5 |
层流理论者认为,流体在转鼓内形成若干同心圆的层流流动,其中自由液面的表层流体流速较大,进入表层的原液可能瞬间进入液室。各层流体的流速随回转半径的增大而减小,沿转鼓壁的流速可能等于零。试验表明,转鼓内存留体积为34L,只有用6倍的液体量才可能将存留液体置换完。可以认为转鼓内少量液体的停留时间可能达到平均停留时间的6倍,甚至更大。
综合分析试验结果,可以认为流体在转鼓内流动同时遵循着活塞理论和层流理论。当在上料过程中上料量未达到液体存留量,即没有达到该转速下的自由液面的形状时,活塞理论起主导作用,表现为活塞式流动。在之后的流动状态将主要表现为层流式,遵循层流理论。
2.3 流体中固体颗粒行为
转鼓高速转动时,料液中极小尺寸颗粒由于布朗运动和转鼓振动的影响,即使在离心力作用下,进入表层料液中的颗粒仍不能沉降而随液流向下流动(遵循层流理论),这些颗粒来不及分离就进入清液室。
脱离开自由液面层的颗粒,在离心力作用下向转鼓壁方向移动,固体颗粒所获得的离心力随着颗粒所处回转半径的增加而增加。固体颗粒径向移动的速度也将随着增大。另一方面固体颗粒也随流体的轴向流动向下流动,但液体流速会随着各层的回转半径的增大而减小。只有当颗粒从自由液面沉降到转鼓壁的时间小于或等于颗粒随轴向向下移动的时间,颗粒才能被截留到转鼓内。
大直径的颗粒具有较大的质量也就获得较大的离心力,大颗粒一进入转鼓即迅速沉降到转鼓壁的上部,质量较小的颗粒具有较小的离心力,随液流向下飘落到转鼓壁的下半程或进入清液。
固体颗粒的沉降分三个过程:起初料液颗粒浓度较小,不同颗粒按照各自的规律自由沉降;当颗粒浓度增加到一定程度形成颗粒群,不同颗粒共同沉降,称为干涉沉降过程;然后固体颗粒叠加到一起后,沉渣密度增加,称为压缩过程。
2.4 理论截留颗粒能力和分离效率
在研究清液质量时,有平均粒径和大粒径三个专用名词:
大粒径是清液中测量到的大粒径的颗粒,也是料液中能够被全部截留到转鼓的小颗粒。
平均粒径指清液中颗粒群名义粒径,可以认为小于平均粒径的颗粒全部进入清液。
平均粒径和大粒径之间的颗粒则部分进入清液,部分截留到转鼓内。
离心机的离心沉降效率与料液有关的参数主要是不溶物固体浓度和料液的液相密度。
离心机截留颗粒物的粒径和分离效率与料液化学组成没有直接的关系。
根据公式计算后,确定离心机及试验液体的具体条件,可能达到的主要参数为处理能力200~300L/h,清液含固量小于5mg/L,截留粒径1.5μm。
3 问题与讨论
3.1 挠性轴沉降式离心机较大振幅及工艺条件选择
由1.1节轴系选择分析可知,挠性轴比刚性轴的振动幅度要大,其转动过程中影响平稳的因素较多,但国外已有应用于生产的成功先例。因此挠性轴沉降式离心机的振动幅度应可控制在能使设备安全温度运行的安全限值范围内。
2004年5月,对吉化集团机械设备有限公司加工制造的挠性轴沉降式离心机系统进行了空载和水负载联动试车,空载试验效果较好,但水负载试验时,选择转速500r/min时上料稳定运行,直至离心机清液口出水,继续提高转速,振动开始明显,当转速达到800r/min时转子振动剧烈,无法正常运转,宣告试验失败。
需要关注的是,在相同的条件下,“干态”运行平稳,在转速500r/min充水后仍能继续运行,但在升速过程中却发生强烈振动的唯一解释是:转鼓在充水后产生了很大的新的不平衡力矩量,即充水后水在转鼓中的分布不均匀,使包括水在内的转鼓在总体上产生了明显的、新的质量分布不平衡力矩量。并且所有激振力产生的振动在某一特定条件下得到了大幅度的加强。
根据各方专业技术人员分析结果,能激发起离心机振动的激振力种类繁多:转鼓结构加工和平衡精度所造成的残余不平衡力矩量;转鼓及其上安装的零部件的装配关系不当(例如各种旋转零件装配不当,松紧度、间隙或同心度超差等),设备运转时也会产生激振力;流体产生 的激振力,例如散液盘的不平度会导致料液分散到转鼓内壁上的入射角度和流量分布都不均匀对称,从而引起转鼓的附加激振力;运行时转鼓内的物料和液体存留可能引发整个转动轴系临界转速和振型的改变,使得原有的激振力对转子振动作用加大。其中临界转速是影响振幅的重要的因素之一,当作用在转子-支承系统上的周期性扰动力的频率(激振频率)等于该系统的固有频率时,该系统就处于共振状态。处于共振状态下的转子的振幅将会扩大。理论上,离心机在加速条件下,大振幅的发生将出现“滞后”现象,即发生在高于临界转速之后,而滞后的程度与加速度大小有关,加速度越高,滞后越多。根据北京化工大学机械工程学院徐鸿教授采用有限元分析方法对两台工程机(吉化,西塘)临界速度的计算,即在转鼓空载下,第一阶临界转速为750r/min,在负载下(充液体积0.034m³,密度为1400kg/m³,充液体质量476.1kg)第一阶临界转速为540r/min。而吉化的试验在500r/min进料,非常接近但低于第一阶临界转速,所以进料过程运行平稳,但随着转速上升,立即经过第一阶临界转速,振幅开始增大,转速持续上升至800r/min,以致振动强烈,引发过载保护开关动作,自动停机。结合试验,综合分析激发振动的各种因素,临界转速的影响是至关重要的。因此需选择合适的工艺操作条件来降低或消除临界转速的影响。选择在大于并远离一阶临界转速的速度下(1200r/min,2000r/min)上料,避免了在进料后,新增激振力在过临界转速时增幅和叠加,这一工艺条件选择在西塘沉降式离心机得到了验证,并且运行良好。
3.2 系统的清洗及去污
沉降式离心机的机架以及上轴系、测量仪表均屏蔽在盖板以上,不与料液直接接触,可以进行直接检修,无需清洗、去污。在屏蔽盖板以下的转鼓、套筒、底锥、渣口切换罐由于能直接与未净化的溶解液接触,放射性水平较高,即使进行远距离拆装时也需先进行清洗去污,降低其放射性水平。
目前沉降式离心机清洗及去污装置有:
(1)位于转鼓上方的解析液环管。Φ25环管在相距20cm间隔向下开槽(1mm×20mm)。每一开槽可向下直线喷淋,主要用于转鼓外壁的冲洗去污。转鼓旋转时,冲洗区域即可覆盖整个转鼓外壁,由于套筒不能旋转,因此环管对套筒的淋洗区域会局限于某几个固定区域,且范围较小。
(2)转鼓内部有高压水喷嘴,必要时上料管也可作为去污用。4个高压水喷嘴呈90°扇形喷射,能覆盖除散液盘上部的转鼓顶部以外的所有区域,但只可加入无离子水不可能加入解析液冲洗。解析液洗涤可以由料液槽经上料管进入转鼓,但也不能冲洗液盘上部的转鼓顶部。
(3)渣口切换罐内上方的解析液环管,结构与转鼓上方的解析液环管相似,可冲洗渣口切换罐内部。
在模拟料液试验过程中发现,在高速分离转速下,清液带滤渣有沿转鼓外壁向上“爬行”的现象,并被甩至套筒内壁,在进行5次模拟料液试验后,整个套筒内壁均有料液痕迹,而且解析液环管上附着有明显的固体颗粒。另外液体与气体摩擦,进料与设备撞击,产生的雾滴或液滴会使整个由套筒和底锥构成的封闭结构内壁粘附料液(包括上料管、高压水管、散液盘),因此上述每一部位如果不能得到很好去污,都会影响总的去污效果。尤其是转鼓上方的解析液环管上积累有明显的固体颗粒,溶解液中不溶性固体颗粒总量为铀的0.1%~0.2%(按质量计),不溶物主要为Ru、Mo等,衰变热为12W/kgU,金属细屑易燃,由于衰变热的产生会使固渣干涸,难于冲洗,并随处理量的增多,积累的干涸固渣的量也会增多,将会带来一系列的诸如局部放射性过高和临界等问题。
从上述的现有的清洗去污装置覆盖范围来看,转鼓上方的解析液环管,套筒,底锥的清液室、散液盘上部的转鼓顶部,以及散液盘的底面(朝下面)都不能获得好的清洗(局部存在清洗“死区”),有待进一步改进解决。
3.3 含渣水进入清液槽(降速过程中)影响分离效率
模拟料液试验发现:在高速分离转速下从清液口出来的清液分离效率达到99%以上,停止上料,待清液口停止流出清液后(模拟过程未进行置换),离心机从高速(2500r/min)降到中速(2000r/min,1200r/min),此转速稳定运行一段时间,从清液口流出来的清液约2L,分离效率小于99%(只有96%~98%)。待清液口停止流出清液后继续降速到低速(20r/min)(降速过程迅速,只需8~10s)。此过程转鼓内残留的液体几乎全部从转鼓流出,约1/3进入清液口,2/3进入排渣口(或回流口),进入清液口和进入排渣口(或回流口)的液体含有大量的固体颗粒。进入清液槽的这部分含渣料液使得沉降分离的总分离效率只有约86%(高速分离阶段分离效率≥99%),不能满足工艺要求。因此如何保证降速过程中含渣料液不进入清液槽是保证分离效率的关键。
从工艺角度考虑:
(1)在离心机清液口至清液槽的管道上增加回流至渣水槽的管道,并分别在流向清液槽和流向渣水槽的管道上增加穿地阀,控制清液和含渣液的流向。
(2)由于在上料和高速分离过程中,料液沿上料管外壁的回流液及形成的雾状液滴汇集液较少(不超过总料液的0.1‰),即使全部进入清液也对总的分离效率影响较小,在此基础上不设置清液口(进入清液室的清液重新进入底锥,可在清液室与底锥连接处开连接口),并在高速分离及酸置换操作时,渣口切换罐的锥筒对准回流口,使得清液通过回流口进入清液槽。在酸置换后需降速时,切换锥筒对准排渣口,转鼓内的残留弱酸和滤渣以及冲渣过程的冲渣水通过排渣口进入渣水槽。
从设备设计考虑,可选择增大底锥的直径或缩小底锥与转鼓溢流口端的距离来解决降速过程转鼓内残液进入清液口的问题。但具体尺寸需经过精确计算和试验验证才能确定。
4 结论
(1)挠性轴沉降式离心机比刚性轴沉降式离心机振动剧烈,影响振动的激振力种类较多,控制零部件加工精度,优化转鼓的内部结构,控制装配误差,都能较大程度地消除不平衡力矩量。其工作转速高于一阶临界转速,存在过临界转速时的共振现象,控制好工艺条件,在高于并远离一阶临界转速的转速下上料,可以降低或消除过一阶临界转速时剧烈振动。
(2)沉降式离心机转鼓内流体的流动状态同时遵循着活塞理论和层流理论。并可计算出液体在转鼓内停留时间和少量液体置换时所需置换液体积。
(3)沉降式离心机转鼓内截留粒径与转鼓转速、料液黏度、固液密度差有关。转速和固液密度差越大截留颗粒能力越强。
(4)沉降式离心机清洗去污存在“死区”,有待改进和解决。
(5)沉降式离心机降速过程中转鼓内残留液携带滤渣进入清液槽,影响总的分离效率,可以通过修改工艺管道、操作方式以及优化设备的结构设计解决。