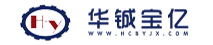
在工业化生产过程中存在着许多的液-固、液-液、液-液-固分离物料,特别是液-固、液-液两相密度差很小或固体颗粒较小的情况下,仅仅采用重力沉降是不能满足要求的,而采用离心分离的方法就很容易得到解决。离心分离可实现连续操作、增大生产能力、提高分离效果、降低劳动强度以及提高生产效率等。碟式分离机具有较高的分离因数,可用来进行净化、澄清和浓缩分离,是高性能的分离机械,广泛应用于石油化工、医药、轻工、船舶、食品等行业。国外碟式分离机的发展迅速,如瑞典Alfalaval和德国Westfalia的碟式分离机在分离技术方面具有国际领先水平。我国碟式分离机是从六十年代初开始,在引进、测绘国外碟式分离机的基础上逐步发展起来,消化吸收了国外先进技术,并通过不断改进创新,形成了具有自主技术的碟式分离机系列化产品。但实际生产过程中经常会出现物料不同分离效果不理想的情况,本文主要从碟式分离机的自身结构、使用工况及过程工艺参数来分析影响分离效果的因素。
一、碟式分离机分离原理
碟式分离机转鼓内有一组碟片,把转鼓空间分成许多薄层分离空间,从而大大缩短沉降距离,改善和提高分离效果。
物料经进料管沿转鼓中心进入分配器,通过分配器孔进入碟片,液体以薄层在碟片间沿径向流动,轻相流向转鼓中心经轻相流道由轻液向心泵排出,重相流向转鼓壁经重相流道由重液向心泵排出,沉渣沉积在转鼓壁上经活塞排渣间歇排出。
二、影响分离效果的因素
2.1 分离机自身结构的影响
2.1.1 分离因数
分离因数是指颗粒在离心力场中沉降速度与在重力场中沉降速度的比,分离因数是分离机分离性能的重要指标,分离机的分离因数越高,物料就越易被分离,分离效果越好。其计算公式如下:
F=w²R/g
式中:w-分离机的回转角速度(r/s)
R-分离机的内半径(m)
S-重力加速度,g=9.81m/s²
从上式可以看出,提高转速比增大转鼓直径更有利于提高分离因数。例如,针对含某菌丝的物料进行分离时,由于菌丝颗粒度在0.5~1μm之间较难分离,采碟式分离机,其分离因数高达10000以上,能够将菌丝从发酵液中分离出来,而用其他离心机就很难达到要求。
2.1.2 碟片分配孔
对于液-液分离,碟片分配孔的位置是影响轻、重相分离效果的一个重要参数。分配孔位置偏向中心或偏离中心,物料进入分配孔就容易破坏已形成的分离液界面,影响分离效果。分配孔位置偏向中心,轻相就会含较多的重相组分,相反分配孔位置偏外,重相就会含较多的轻相组分。
2.1.3 碟片间距
碟片间距应使物料中的颗粒在碟片间运动时来得及穿过液流面达到上碟片的下表面;同时在碟片表面沉降临界直径的颗粒不会重新被液流所带走。
2.1.4 碟片半锥角
碟片半锥角即碟片母线与轴线的夹角α应满足tanα>f的条件,f为沉渣对碟片表面的摩擦系数。α角太小,颗粒贴在碟片下表面不能分离,一般在30°~45°范围内。
2.1.5 碟片表面粗糙度
液体在高速旋转的转鼓内流动是较为复杂的湍流流动,碟片表面的粗糙度影响液体的流动,表面摩擦系数f增大也将阻碍颗粒在表面向外圆的移动。表面的粗糙度越大,摩擦系数增加,流动阻力增大,改变颗粒在碟片间流动的路线,就会导致一些理论上能分离出来并能到达上碟片下表面的颗粒不能到达碟片外圆,而被液流带走,影响分离效果。例如碟片在实际生产中采用旋薄技术成形,碟片的内外表面比采用冲压成形碟片光滑,较大限度地降低碟片表面粗糙度对流体的影响。一般来说,碟片内外表面经抛光处理后,其粗糙度不大于1.6μm。
2.2 分离机的使用工况及过程工艺参数的影响
2.2.1 重力环口径
调整重力环口径就是改变重相出口口径,调整轻、重相的分离界面,使物料进入碟片分配孔分离时不致破坏已形成的分离界面,以达到较佳的分离效果。重力环口径变大,由于轻、重相离心液压的平衡,分离界面往碟片外移动,轻相中含重相就越少;反之重力环口径变小,分离界面往碟片中心移动,重相液含轻相就越少。
2.2.2 液位环口径
调整液位环口径就是改变轻相出口口径,调整轻、重相的分离界面,使物料进入碟片分配孔分离时不致破坏已形成的分离界面,以达到较佳的分离效果。液位环口径变小,由于轻、重相离心液压的平衡,分离界面往碟片外移动,轻相中含重相就越少;反之液位环口径变大,分离界面往碟片中心移动,重相中含轻相就越少。
2.2.3 出口压力
出口压力用来调整轻、重相的分离界面,增加轻相的压力就会将分离界面向重相层方向移动,得到澄清的轻相。反之,增加重相的压力就会将分离界面向轻相层方向移动,得到澄清的重相。
2.2.4 排渣时间间隔
对于间隙排渣碟式分离机,其排渣时间间隔要根据物料含固量的多少来确定,如人工除渣分离机要定期进行清渣处理,部排或全排分离机要定期进行排渣操作,否则固相会积满渣腔,甚至会堵塞碟片间隙,影响分离效果。
2.2.5 物料分离温度
温度对物料分离的影响是很大的,物料黏度是随温度变化而变化的。温度升高,物料的粘度降低,越有利于物料的分离;温度降低,物料的粘度升高,就会影响物料的分离。因此温度的控制有利于分离过程的稳定,应避免产生波动。尤其对粘度随温度变化较大的物料,温度的控制至关重要,例如重油的分离温度在95℃~98℃、植物油的分离温度在85℃~95℃,才能使碟式分离机达到较佳的分离效果。
2.2.6 物料的搅拌
悬浊液的分离需进行充分搅拌,混合均匀,同时使固体颗粒均匀分散在料液中。对于在生产过程中形成的颗粒状物质,搅拌缓和均匀不致使形成颗粒被打碎而影响分离效果。选择合适的搅拌速度和搅拌翅对物料的分离效果起着重要的作用。例如在植物油精炼中的水化脱胶过程中,植物油碟式分离机是利用植物油中磷脂等胶溶性杂质的亲水性,吸水凝聚成颗粒去除植物油中胶溶性杂质,植物油进碟式分离机分离前,经水化罐并不断搅拌使磷脂充分凝聚,若搅拌不充分,磷脂不能完全凝聚,或者搅拌剧烈,磷脂凝聚成的颗粒易被打碎,经分离后磷脂(即重相)含油率28%~32%。若通过水化罐的减速机将搅拌速度控制在70~90r/min,经分离后磷脂(即重相)含油率降至25%~28%。因此通过对水化过程搅拌强度的控制,来提高碟式分离机的分离效果,提高植物油精炼率。
2.2.7 进料稳定性
保持进料稳定很重要,必须避免产生波动,进料的稳定在一定程度上保证了分离界面的恒定,一旦产生波动就会破坏分离界面,影响分离效果。
三、结束语
碟式分离机对物料分离效果的好坏,是各种参数相互制约的结构,液体在碟片间流动情况及粒子在碟片间运动情况相当复杂,不仅受到离心加速度的影响,同时还受到哥氏加速度及液体粘滞阻力的影响。分离机自身结构的影响还需要在实际应用过程中不断探索和积累经验,根据不同物料确定其结构。同时分离机的使用工况及过程工艺参数需要进行调整,选择合适的工况以及合理的工艺参数才能达到较佳的分离效果。