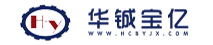
1 前言
某炼化企业污水处理厂在生产过程中,通过分析离心机工作原理,结合生产实际情况,总结出影响离心机脱水效果的各种因素。影响离心机分离效果的因素主要包括不可调节的机械因素、可调节的机械因素。其中不可调节的机械因素在设备选型前期根据现场物料情况给出具体参数,选择了符合生产实际的D5LL型离心机。本文重点分析在实际生产过程中,影响离心机脱水效果的可调节的机械因素,为离心脱水机的生产维护提供理论基础。
2 不可调节的机械因素
2.1 转鼓直径和有效长度
离心机的转鼓直径和长度是影响分离效果的重要因素,转鼓的直径和长度与离心机处理能力成正比,随着转鼓直径和长度的增加,物料在转鼓内沉降分离的面积增加,物料停留的时间也随之增加,在转鼓转速相同的情况下,大直径和长转鼓的分离效果明显提高。因此,在同等情况下,选择大转鼓直径可以提高离心力,并且可以降低转鼓转速,节约电耗。但是,离心机的转鼓直径也不能毫无根据地增加,由于受材料的限制,离心机的转鼓直径是有极限值的,一般情况下离心机的转鼓直径控制在200~1000mm。D5LL型离心机转鼓长度为4570mm、转鼓直径为1090mm,经过长周期运行证明,符合现场生产实际情况,较好地实现了污泥脱水效果。D5LL型离心机采用的大直径转鼓可以实现较低的差速运行,大直径转鼓的螺旋刮泥能力也随之提升,在相同的排泥量下,小直径转鼓的离心机只能提高差速,减少分离沉降时间,以致脱水效果不佳,因此大直径转鼓的离心机分离效果较好。
2.2 转鼓半锥角
离心机在运行过程中,螺旋输送器将已经脱水的固环层不断推向出泥口,螺旋推力的扭矩大小由转鼓半锥角的大小决定,半锥角越大,脱水后的污泥受到的离心力和挤压力也越大,脱水后的污泥容易产生回流,排泥变得困难,严重时会造成螺旋叶片磨损。反之,半锥角越小,物料在转鼓分离的有效面积也越小,影响着离心机的分离效果。当转鼓内的物料深度固定时,如果转鼓半锥角增大,则会导致污泥脱离液面到排泥口的距离缩短,这将会使污泥的脱水时间缩短,脱水后的污泥含水率增高,但是,转鼓的沉降区长度则会加长,物料在转鼓内的分离沉降面积增加,污泥脱水后的澄清液会更加清澈。相反,如果转鼓半锥角减小,将会导致污泥的干燥区长度增加,污泥的脱水时间也随之增加,排泥的含固率增加。
转鼓半锥角是离心机选型的一项重要参数。作为炼化企业的污水处理厂,脱水离心机的运行首先要保证出泥含固率,要选择合适的转鼓半锥角来适应现场的实际需要。一般情况下,为保证污泥能够顺利排出,转鼓半锥角设定为10°以内。D5LL型离心机转鼓半锥角为8°,能够满足生产需要。
2.3 螺旋类型
螺旋输送器也称螺旋,螺旋作为输送沉降污泥并排泥的离心机卸料装置,影响着离心机的脱水效果和处理能力。D5LL型离心机的螺旋输送器采用安德里茨专利技术设计制造的多性能转子,采用中空式设计。采用这种设计可以实现较好的固液分离效果,在排出澄清液的过程中减少对固体的干扰。这种新型的螺旋排出的澄清液顺轴向直接排出,也可缩减澄清液排出的行程。
2.4 螺距
螺距是螺旋输送器相邻的两个叶片之间的距离。作为离心机的一项非常重要的结构参数,决定着污泥排泥的成功与失败。在螺旋输送器的直径固定时,螺距越小,与之对应的螺旋升角越小,污泥在螺旋叶片间就越不容易堵塞。另外,减小螺距可以增加螺旋叶片的圈数,可以避免转鼓锥端物料分布不均,从根本上消除机器振动的现象。所以,对于不容易分离的物料,例如活性污泥等,排泥比较困难,螺距选择趋于小一些,通常为转鼓直径的1/5~1/6。对于比较容易分离的物料,螺距选择会大一些,通常为转鼓直径的1/2~1/5,从而提高污泥的排泥能力。D5LL型离心机的螺距为260mm,对于现场的活性污泥和化学污泥能够起到较好的输渣效果。
3 可调节的机械因素
3.1 转鼓转速
离心机依靠转鼓的高速旋转产生强大的离心力,在离心力的作用下实现物料的分离,因此,转鼓转速越高,离心力越大,分离效果越好。但是,经过实践证明,过高的转速会导致污泥絮凝剂遭到破坏,絮凝剂的絮凝效果明显降低,进而导致污泥脱水效果的下降。另外,较高的转鼓转速对离心机的破坏力也随之增加,材料的磨损、机械部件的损坏、设备振动和噪音都会不同程度的增加。
转鼓转速和离心机的分离因数有关,分离因数是离心机内物料所承受的离心力与所承受的重力的比值。分离因数是离心加速度和重力加速度的比值,它反映了离心机分离能力的高低,也是离心机非常重要的一项参数。通常情况下,分离因数和离心机的分离效果成正比。
D5LL型离心机在投用初期,为获得较佳脱水效果,将转鼓转速设定为3000r/min,低于安全转速3200r/min,并实现连续长周期平稳运行。但是离心机属于高速旋转设备,由于螺旋磨损、停机冲洗不彻底等原因都会导致产生振动及噪音,甚至出现轴承损坏情况。
3.2 差转速
差转速也称差速,是转鼓和螺旋之间的速度差,同转鼓转速一样,差速也决定着离心机的分离效果。离心机在运行时,转鼓在高速转动时产生一个强大的离心力,在离心力的作用下,污泥颗粒被分离在转鼓的内壁上,脱水后的污泥成环状,离心机的控制系统会根据转鼓内的扭矩情况,调节转鼓和螺旋输送器之间的差转速,然后通过螺旋输送器的推进,脱水后的污泥从排渣口排出,从而完成固液分离。在D5LL型的控制系统中设定差速1~12r/min。
根据离心机的机械结构和工作原理分析,提高速差,可以加快转鼓内的污泥排出速度,但是会缩短污泥在转鼓内的沉降时间,造成排出的污泥含湿率较高,无法形成泥饼,给污泥的运输造成不便,而且过高的差速会导致螺旋干扰澄清液,造成澄清液质量下降。反之,降低速差,可减缓污泥的排泥速度,增加污泥在转鼓内的停留时间,提高分离效果,脱水后的污泥含湿率较低,污泥成饼状,方便运输,并且减小螺旋对澄清液的干扰,提高滤液的清洁度。理论上差速越低,分离效果越好,污泥干度越高,但是过低的差速会导致污泥含湿量明显下降,增加螺旋输送器的排泥负荷,造成排泥不畅,严重时会发生堵料现象,给离心机的运行带来冲击,螺旋输送器的磨损明显加快。
在运行过程中,如何保证污泥的脱水效果,差速调整非常关键,过高或过低的差速都不适合生产需要,结合污泥的特性、离心机处理能力和处理要求,探寻差速的较佳值是离心机运行管理的一项重要内容。一般认为泥饼在干燥区的脱水时间应控制在4~6s,时间再加长效果增加不明显。按照操作规程,差速器给出的范围在1~12r/min,在自动控制系统中设定差速1~12r/min,系统会根据离心机内物料的扭矩情况自动调节差速,满足分离要求。
在离心机运行过程中,进泥量和进泥浓度通常变化不大,当转鼓转速固定,絮凝剂消耗保持一定范围时,离心机的脱水效果和处理量主要受差速的影响。
3.3 液环层厚度
液环层厚度同样是影响离心机运行效果的重要工艺参数,离心机运行时是无法调节的,只有当离心机处于停车状态时,手动调节液位挡板,从而控制液位的高低,在调整挡板时,务必保证离心机的每个挡板都处于同一水平位置,避免离心机高速运转时产生剧烈振动。D5LL型离心机的液位挡板设置在离心机螺旋的出料端,使得离心机的液位足够深,这种结构的挡板经过优化设计,分离能力得到提升,在运行过程中节省了药剂的消耗,并且降低了污泥的含水率。调整液位挡板可以实现液环层厚度的控制,从而实现对排泥含湿率的控制。
4 结论
详细分析了影响离心机脱水效果的各种因素,主要分为不可调节的机械因素、可调节的机械因素和工艺因素。其中不可调节的机械因素包括转鼓直径和有效长度、转鼓半锥角、螺旋类型和螺距。可调节的机械因素包括转鼓转速、差转速和液环层厚度。由于不可调节的因素在设备选型时已经确定,在可调节的机械因素中,液环层厚度必须在开车前完成设定,运行中无法调节,因此,在离心机的运行过程中,重点将对转鼓转速和差速度进行调控。