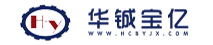
碟式分离机利用薄层分配原理来优化离心过程,适用于不同比重的液-液、液-固、液-液-固等物料的分离,被广泛应用于植物油连续精炼的脱胶、脱皂、水洗等工艺中,是现代油脂精炼的主要设备之一。
碟式分离机主要由机身、机盖、转鼓、横轴、立轴、进出口装置等部分组成,工作核心部件为转鼓,被安装于立轴之上。转鼓内有多层碟片,按顺序装在分配器上,碟片及分配器的分配孔上下对齐,形成几条进液通道(中性孔)。碟片之间用定距条隔开,转鼓内分成许多薄层分离空间,从而大大缩短沉降距离,改善和提高分离效果。工作中待分离的混合油脂均匀进入转鼓内部,在转鼓高速转动而产生的巨大离心力作用下,混合油经中性孔进入碟片束的分离间隔中,比重较大的物料(磷脂、皂脚、水等)被离心力抛向转鼓内壁,流动性较好的油沿着转鼓盖和碟片压盖间的通道向上运动,由大向心泵排入重相出口,而少量油泥等重渣会积聚在沉渣区,周期性自动排出或停机后由人工清理。而比重较小的物料(轻相)被迫沿碟片内缘入中间通道,向上由小向心泵排入轻相管道。国产及进口大产量碟式分离机的重相向心泵多设计为可调式,其大小的变化可改变转鼓内轻、重相的分离界面,获得不同的分离效果。
用于油脂精炼工艺的碟式分离机现今有多种品牌及规格,但分离工作原理基本相同,下面以国产DHZ470型自清式碟式分离机为例,从工艺的角度就保证碟式分离机能稳定工作应注意的若干问题进行探讨。
1 碟式分离机的就位及拆装
碟式分离机的地脚以浇铸为宜,4个地脚螺栓应与车间楼面内的钢筋焊接相连,在浇铸之前务必校验4个地脚的水平。当多台分离机安装时,应保证所有转鼓中心在同一线上,并且基础之间应有足够操作空间以保证转鼓或横轴的拆卸及安装。分离机上方用于安装电动葫芦的工字钢应牢固水平,电动葫芦的吊钩中心应在多台分离机转鼓的中心联线上。实践证明在吊装转鼓时,将一小手拉葫芦挂在电动葫芦的吊钩上,人工慢慢吊装转鼓,能有效保护转鼓与立轴的结合锥面,减少对立轴轴承的冲击,延长分离机使用寿命。为不影响分离机的动静平衡,生产厂家在设备出厂前在相关部位都打上装配标志,装配不到位是不允许开机运行的,否则可能造成严重后果。
2 碟式分离机开车的基本外部要求
除供电应达到运行要求外,还有其他几个要求。首先是对毛油的质量要求,进入工艺中的毛油中固杂含量应控制在0.2%以下,较低的含杂量是使分离机能长期稳定工作的因素之一。当油中的固杂含量过高超出了自清分离机周期排渣的能力时,不断增加的杂质会累积在转鼓内,使转鼓内有效工作容量减少,轻重相分离效果变差,影响油品的产量及质量,严重时会很快堵塞转鼓,增加停机清理的次数。值得注意的是刚开始进油时,建议用新的、干净的毛油,尽量不用炼过的回油,因为回油内含水量一般过高,并且油品的物化性质不均,加水、加酸或加碱的量不能很好把握,这样的油如果再进到分离机内进行分离,不能快速形成很好的分离界面,反而更易出现严重的分离不清或重相跑油现象,会造成较多的油品损失,甚至又会产生更多的难处理的回油,形成恶性循环。当采用品质稳定的毛油分离达到正常后,再逐步少量的把回油掺入毛油中,平稳地把回油炼完。
分离机对水的要求也非常严格,转鼓冲洗水(包括热机水)及洗涤油脂水均应为软水,对控制转鼓自动排渣的操作用水也要求为软水,甚至用于配置碱液的水也应为软水。软水的各项指标应达到锅炉用水的要求。因为硬水中的盐类会在分离机的碟片、大小活塞、转鼓内外壁上结垢,影响转鼓的动平衡,尤其是转鼓内大小活塞的结垢会造成活塞运动不灵活,使自动排渣失常,严重时必须停机清洗。造成油品的损失及连续生产不正常,而且硬水在工艺中还会影响脱胶、脱酸及洗涤油中残皂的效果,影响油品的质量。控制转鼓自动排渣的操作用水建议采用冷软水,这更利于达到大小活塞内较少结垢的要求及延长密封圈工作寿命,使分离工作长时间稳定。热水及冷水管道上应装有过滤器,尤其是在进自动控制的电磁阀前务必安装有细网过滤器,避免因大杂物卡在电磁阀内而影响分离机的正常排渣。碟式分离机的操作用水建议采用单机单泵方式供给,单独从冷的软水罐中泵出,不建议与工艺热水共用热水泵或多台分离机共用一泵,因为实际生产中可能会造成操作水压不稳,影响分离机的正常工作。为利于操作水压的平稳性及易调性,保障分离机排渣连续正常,操作水泵选用小流量大扬程的多级离心泵或旋涡泵等,操作水压一般在0.2~0.4MPa之间可调。
3 碟式分离机的起动及工作
在确认分离机安装到位及毛油、热水、操作水、酸、碱等相关工艺条件准备就绪的前提下,起动分离机,国产DH470自清式分离机的一般起动时间在6~10min,起动电流瞬间可达70~80A,到全速后电流一般在20A左右,当通入操作水后转鼓内大活塞密封,这时分离机工作电流还会变小一些。可慢慢向转鼓内通入少量热水,并观察电流表的变化,如果在加入少量水后电流变化很大且逐渐升高,说明转鼓密封未完全,应停止进水,进行一个或多个手动排渣后再观察。如加水后上升的电流很快下降并正常,说明转鼓大活塞已经密封好,调整自控仪上的排渣时间,通过运行手动排渣,达到理想的排渣效果,连续加入热水对分离机进行热机。
在准备进油之前先把转鼓排渣的周期调长一些,建议在30min以上,主要是避免刚进油后可能会使分离机排渣跑油。分离机准备进油时应格外小心,建议初进的油经加热器时不要加热,当看到分离机的重相口(先进行短混工艺)没有较多水流出时,说明转鼓内已经充满油,这时可加入酸碱及升高油温。在进油量、加碱、混合及油温都正常稳定的前提下,通过调节轻相管道处的背压阀,慢慢使压力在0.2MPa左右,同时仔细观察轻相及重相的分离效果。当分离正常后调小自控仪上的排渣周期,一般在5~15min之间。这时还应多注意几个部分排渣的操作,看排渣是太大还是太小,当出现排渣跑油时说明排渣量可能大了,这时可把排渣量调小一些再观察,直到满意为止。排渣量太小起不到自清的效果,但排渣量过大又容易造成排渣跑油,调节自控仪上的排渣时间、改变操作水的压力或流量都会对转鼓的排渣动作产生影响。当毛油很干净且磷脂含量很少时分离机更易跑油,这时可适量减小排渣量及延长排渣周期。如果自清式DHZ470分离机用在脱皂后的水洗工艺中,在部分排渣过程更易跑油,可延长排渣周期在30min以上,适当缩短排渣时间。分离机稳定工作后,可把刚进油时分离不好的回油少量、多次掺入新毛油中,连续平稳地把这些回油炼完。
当碟式分离机加工棉籽油等排渣量大及皂脚多的油品时,应适当调长排渣周期中的冲洗时间,否则可能造成因排渣量大,大量排渣不能及时冲出而堵塞甚至抱死转鼓,因电流升高而自动停机。
4 碟式分离机的停机及清洗
当分离机连续生产多日后发现分离效果逐渐不好或再次启动时机身晃动较大时,可进行分离机的停机清洗工作,分离不好表现为轻相油透明度降低,重相皂脚(磷脂)量减少且落下间隔变长,分离出的洗涤水中含油升高等。这时停止进油泵,终止酸碱的定量加入,停止混合设备,关闭蒸汽阀门等,打开轻相口的污油阀后关闭清油阀,再关闭分离机进油阀门,打开热水阀向转鼓内进水,对分离机进行几次手动部分排渣,不建议使用全排渣方式。切断分离机电源,不使用手动刹车,让机器慢慢停止转动,大约需2h的时间。
在生产中当发现分离效果不好时,在排除其他外围因素情况下,部分操作人员为使连续生产不间断,会采取短时间停止进油,对分离机转鼓内进水冲洗,并连续手动排渣几次,甚至进行一、两次大排渣,这些方法能短时间延长工作时间,但不能真正解决问题。因为自清分离机的排渣不是绝对彻底的,随着时间的延长,转鼓内的油泥会越来越多,用水冲洗只能把皂脚等易流动的物质冲走,而油泥等固杂几乎不能被冲走,随着工作时间的增加,没有被排出的油泥会沉积在分配器下面,大活塞上表面,在转鼓排渣区以上的内壁上都会沉积较多的油泥,甚至在向心泵盖内侧也会沉积较多油泥。这些油泥用热水冲洗或排渣几乎是不能去除的,因此重相分离通道会逐渐变小至堵塞,从分离效果来看轻相会变的不清,虽背压调高,重相的皂脚也不理想。因此应当判定是因为分离机转鼓内沉渣较多而影响分离效果时,就应马上停机清洗转鼓。
实践中打开待清洗的转鼓,会发现转鼓内的沉积物主要为油泥,一旦沉积在排渣口区较远的地方,很难再靠排渣方式排出,而且会越积越多,变得又干又硬,因此必须严格控制毛油中的固杂含量。
当工作较长时间的分离机停机后,虽然转鼓内不是很脏,但建议还是打开进行清洗。因为转鼓内的沉杂在分离机运转时,自然平衡分布,而当分离机一停后,转鼓内的固杂会自然散开,破坏了已形成的平衡,再开机时会出现分离机振动过大的现象,严重时会对轴承造成破坏。
对于分离机的拆装要格外小心,多台同型号的分离机不要同时拆装,容易造成零件的混装,造成严重后果。装配时严格按零件上的钢印标记顺序安装,注意转鼓内的沉渣不要用金属工具来刮,以免破坏转鼓的平衡及内壁与碟片的光滑度。
5 影响碟式分离机工作的其他因素
在油品方面,磷脂含量较高酸值较高的油品分离机重相成形好,排渣不容易跑油,皂脚吸附色素效果好,清相易清,相对来说好炼一些。对于磷脂含量少且酸值低的油品用自清式分离时要多小心,特别是处理四级油或车间回油时更要小心操作,实践证明起初进油时的操作很重要,当分离机调稳后,后面的操作就相对轻松一些。
(1)在油温方面,采用不同的工艺对分离效果也不相同,短混工艺采用高温(85℃~95℃)快混方式能达到好的分离效果,当油温过低时会出现分离不好及重相跑油现象。而采用低温长混工艺时,经预混的加碱油在30℃~50℃的温度下,在延时反应罐中长时间充分反应,之后快速升温后进分离机后同样达到高效的分离效果。如在高温下进行长混,可能会出现大量油脂的皂化现象,分离机不能分离。关于两种工艺对油品及精炼率的影响本文不进行比较,只强调油温对分离机的影响。
(2)在水温方面,无论是在分离机热机时还是稳定工作时,水温都要求较高温度,一般要求水温要高于油温。实践证明,当较低水温热机或热机时间不够时,进油后易出现重相跑油现象。正常生产中,较低的水温会影响水化及水洗效果,使分离不清或重相跑油。
(3)在加酸、加碱或加水等混合效果方面,充分有效的混合不但有利于油中化学及物理过程的充分反应,还利于皂脚(磷脂)的凝聚及色素的吸附等过程,分离效果好,工作也就稳定。
(4)在加碱及加水量方面,都要求适量,加碱量过多会造成中性油损失,产生油品皂化现象,影响加工的精炼率,并直接影响分离机的分离效果。当进行水化脱胶工艺时,加水量不足会造成分离出的磷脂很干,不易分离,而且未参加反应的部分磷脂会跑到后面的离心机中,如正进行水洗时则会出现乳化现象,轻则轻相分离不清,重则重相乳化跑油,影响生产的正常进行。分离机在进行水洗时,加水量一般为油重的10左右,加水太少起不到水洗的效果,影响后面的工序,加水太多不但会影响分离机的产量,还会造成软水的浪费,增加废水的排放量和处理的负担。
6 常见故障的分析及解决
关于分离机的振动过大的问题,可能是由于装配不到位,弹簧、轴承或传动齿轮等机械零件的损坏,转鼓长时间使用而未做动平衡,生产中排渣不充分或上次转鼓内沉渣没有清理等原因。
关于分离机的重相跑油,无论是国产还是进口分离机,如操作不当都会出现跑油现象。造成跑油的原因非常多,直接原因是转鼓中没有形成稳定的分离界面或分离界面突然遭破坏,分离界面向重相面移动,大量油从重相向心泵排出。分离机刚进油时很容易出现跑油现象,热水温度低或热机时间不够,油品物化性质不稳,进油流量不稳定,油温较低或加热不稳,油与管道中的大量水混合造成油品乳化现象,轻相油管上的背压调的过高等,这些都会造成分离机的重相跑油。因为刚进的油品比重不容易稳定,因此刚进油时的操作是非常重要的。在碟式分离机正常工作情况下,有时因排渣的突然变大一下打破了原先已形成的分离平衡,会出现部分排渣后重相跑油。增大排渣时间或缩短排渣周期,提高操作水的压力或调大进水阀门,增加进油量或调高背压压力,连续几个手动排渣,油温、水温降低,因使用硬水后小活塞突然灵活,这些因素都可能造成排渣跑油。在分离机工作中也可能出现非排渣跑油现象,油品的性质突然改变,突然增加产量或调高背压压力,油温、水温变低等都可能造成生产中非排渣跑油。当发生小活塞内阀芯及密封圈损坏或大活塞(滑动活塞)密封处泄漏时,分离机也会出现跑油现象,而且大活塞密封不严造成转鼓跑油,会伴随重相口的跑油及分离机电流的升高。实际生产中我们应做到少跑油或不跑油,除因大小活塞等密封件损坏而造成的跑油外,对于一般跑油处理,直接的方法是向转鼓内冲入热水,隔离轻相使其回到小向心泵,这时轻相背压升高至正常。同时认真检查影响分离效果的各种因素,如调整不好,不管怎样用热水冲也不能达到连续平稳工作的目的。
当出现分离效果不好时,首先要检查是否出现外部条件,油品太脏,加水或加碱量不合适,油温或水温不合适,油与碱或水混合不充分,轻相背压是否调得过低等问题。另外因分离机运行时间过长而使转鼓内沉渣过多也会造成分离效果不好。
对于分离机电流过高现象,如是起运电流过高,可检查横轴部分液力耦合器里的油量是否过多。如运转中非排渣情况下电流过高,一般会伴随有转鼓泄漏发生或机内零件摩擦(如向心泵部分),这时应停止进油,如发现转鼓泄漏则用水冲洗分离机,进行几次手动排渣。如是转鼓泄漏,就要停机进行检查。如不是转鼓泄漏则立即停机检查,看向心泵部分是否有擦痕,如有则根据情况调好它们之间的间隙。
当排渣不理想或不能排渣时,在调整操作水压或流量、改变排渣时间等因素后还不理想,就要检查生产用水,如果操作水达不到锅炉用水的要求,生产一段时间后会在小活塞内结垢,使排渣动作忽大忽小,甚至使阀体泄水孔堵塞,不能排渣,造成频繁停机清洗,影响正常生产或不能生产。当大活塞(滑动活塞)或小活塞的密封圈损坏时,排渣也不理想。转鼓与大活塞(滑动活塞)的结合面太紧也会影响排渣效果。
总之,在实际生产中,影响分离机稳定工作的因素多在外部,人们常说的碟式分离机有问题大都不是其本身机械部件的故障,作为一台被动地执行分离操作的机器,分离机安装、装配到位及空运转正常都只是分离工作的前提,要保持分离工作稳定,更需要调整好外部因素,创造易于分离机工作的条件,使外围油的品质、水品质、进油量、油温、水温、操作水压、反应及混合的效果等因素都达到工艺要求,这样才能长时间稳定地发挥碟式分离机在油脂精炼工艺中的优秀分离性能。